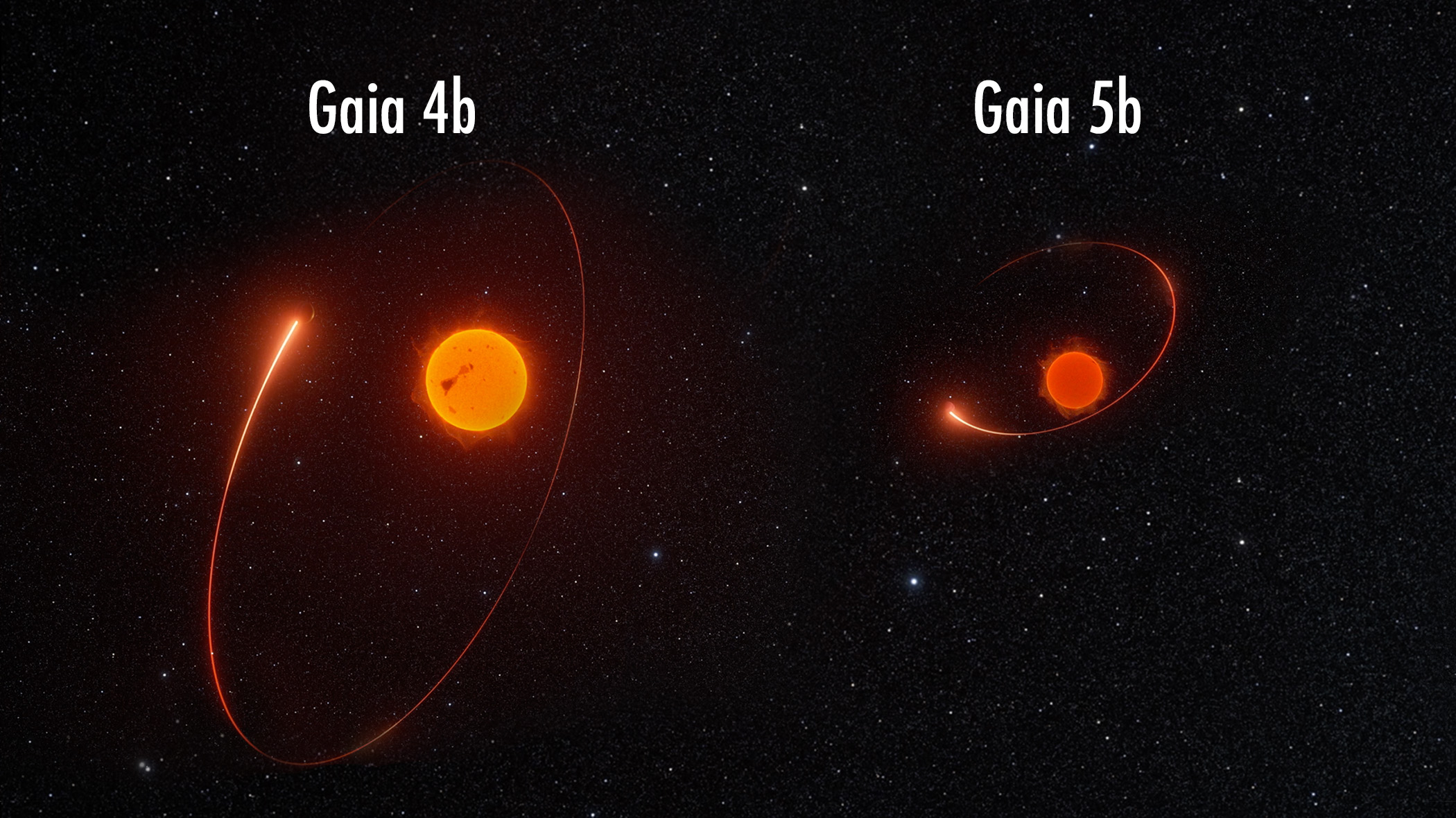
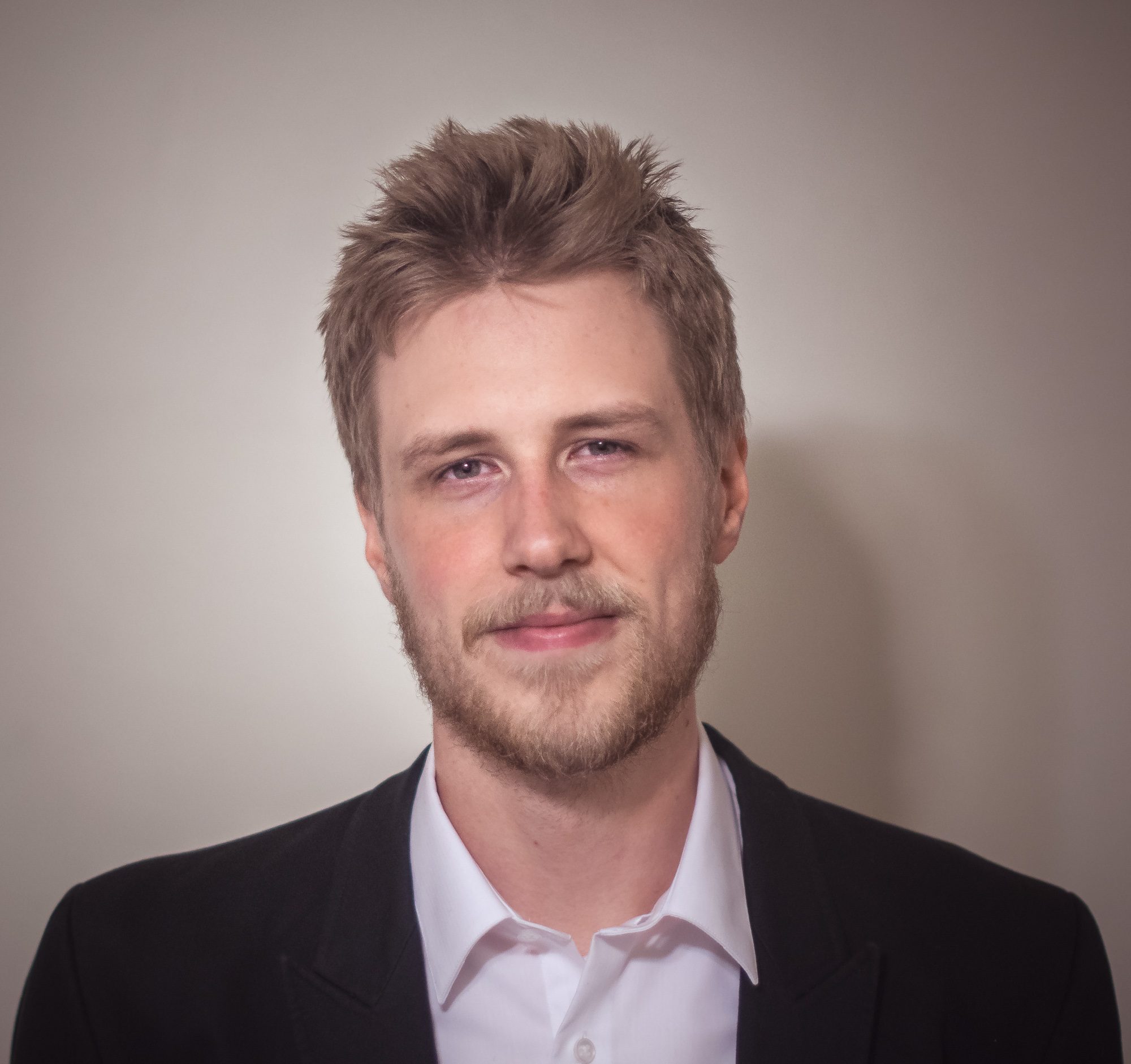
Guðmundur K. Stefánsson, PhD
I am an assistant professor in Astrophysics at the University of Amsterdam.
I work on developing and using next-generation instruments to discover and characterize exoplanets around nearby low-mass stars.
If you are interested in working on exoplanets around low-mass stars, reach out!
Research: Observation
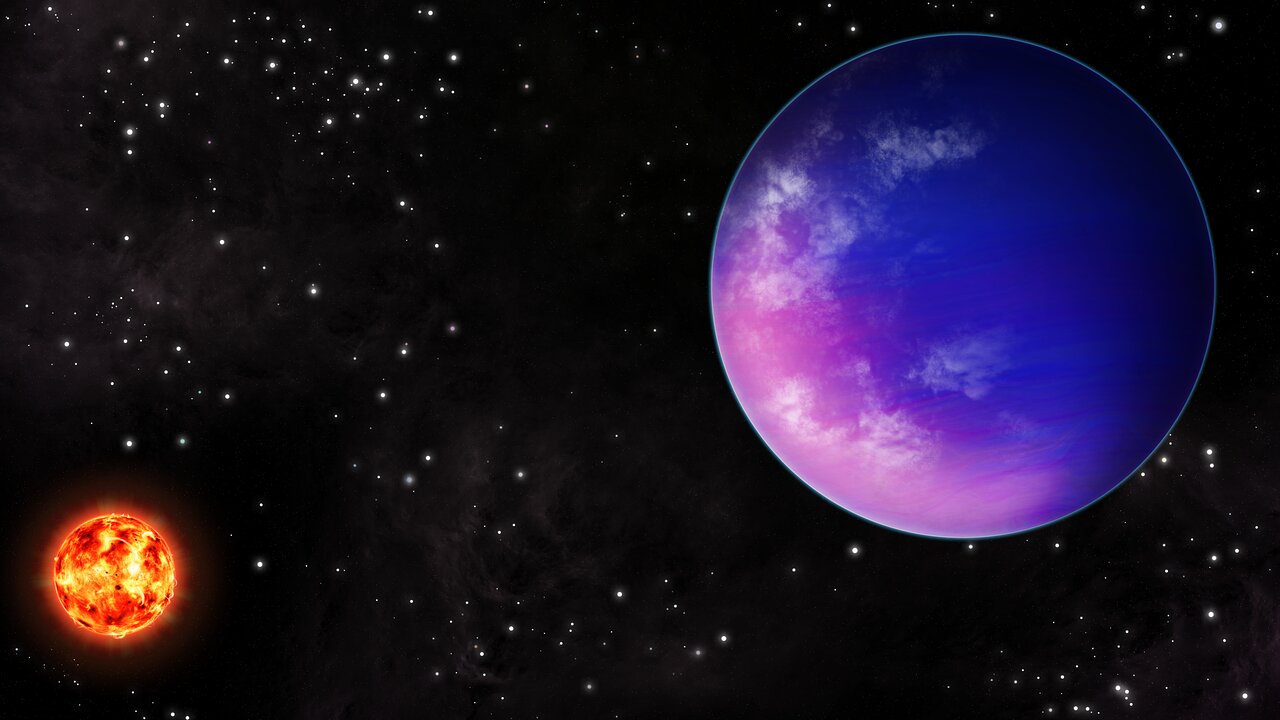
Discovering New Planets Orbiting Nearby M-dwarf Stars
Using diffuser-assisted photometry and precision radial velocities with HPF, I have led or directly contributed to a number of efforts to detect and characterize new planet candidates orbiting nearby stars, with a particular focus on planets orbiting nearby M-dwarfs.
Relevant Papers:
- Stefansson et al. 2020a: Detection of the nearby M-dwarf planet G 9-40b, an excellent target for transmission spectroscopy.
- Stefansson et al. 2020c: Detection of the TOI-1266 system, a two planet M-dwarf system where one planet is in the radius valley.
- Cañas et al. 2020: Detection of TOI-1899b, the first Warm Jupiter orbiting an M-dwarf.
- Kanodia et al. 2020: Detection of TOI-1728b, a hot Supter Neptune orbiting a nearby M-dwarf.
- Cañas et al. 2019: Detection of TOI-150b, a Hot Jupiter in the TESS Continuous Viewing Zone.
Discovering Astrometric Planets from Gaia
ESA's Gaia spacecraft is expected to detect hundreds if not thousands of planets in the near future. In our recent paper, we have detected some of the first astrometric planets and brown dwarfs from the Gaia spacecraft which are called Gaia-4b and Gaia-5b. This marks the tip-of-the-iceberg of the numerous planet detections to come from Gaia.
Relevant Papers:
- Stefansson et al. 2025: Detection of Gaia-4b and Gaia-5b, some of the first astrometric substellar companions detected with Gaia astrometry.
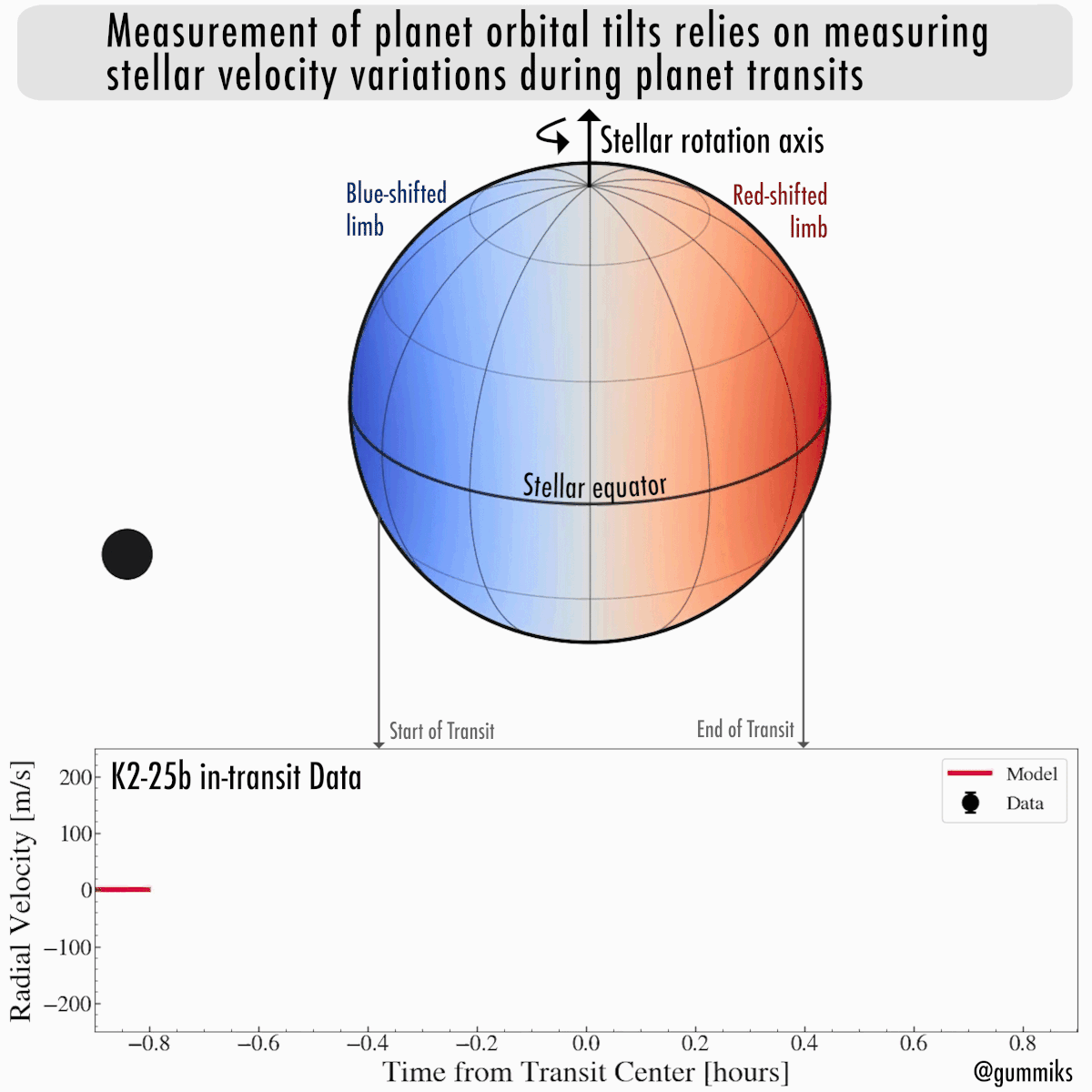
Characterization of the Properties of Nearby M-dwarf Planet Systems
Using diffuser-assisted photometry and precision Radial Velocities (RVs) with HPF and other spectrographs, I am currently leading efforts to study the orbital and atmospheric properties of planets orbiting nearby M-dwarfs.
In particular, I am interested in using the Rossiter-McLaughlin Effect to characterize the spin-orbit alignment of planets, a powerful probe of their formation and subsequent dynamical evolution. As is shown in the animation to the left, this method relies on measuring the angle between the stellar rotation axis and the stellar equator. As a star rotates, one hemisphere is blueshifted towards the observer, and the other hemisphere is redshifted. As a planet crosses in front of the stellar disk, the planet successively blocks differently blue and redshifted light from the star resulting in a detectable signature in the RVs during the transit. The shape and size of this signature is strongly sensitive to the obliquity of the planet, the angle between the stellar equator and the planet orbit.Relevant Papers:
- Stefansson et al. 2022: The Warm Neptune GJ 3470b Has a Polar Orbit.
- Stefansson et al. 2020b: Characterization of the young hot Neptune planet K2-25b orbiting an M4.5-dwarf in the Hyades.
- Stefansson et al. 2018a: Diffuser-assisted characterization of the Neptune-sized planets K2-28b and K2-100b.
Research: Instrumentation
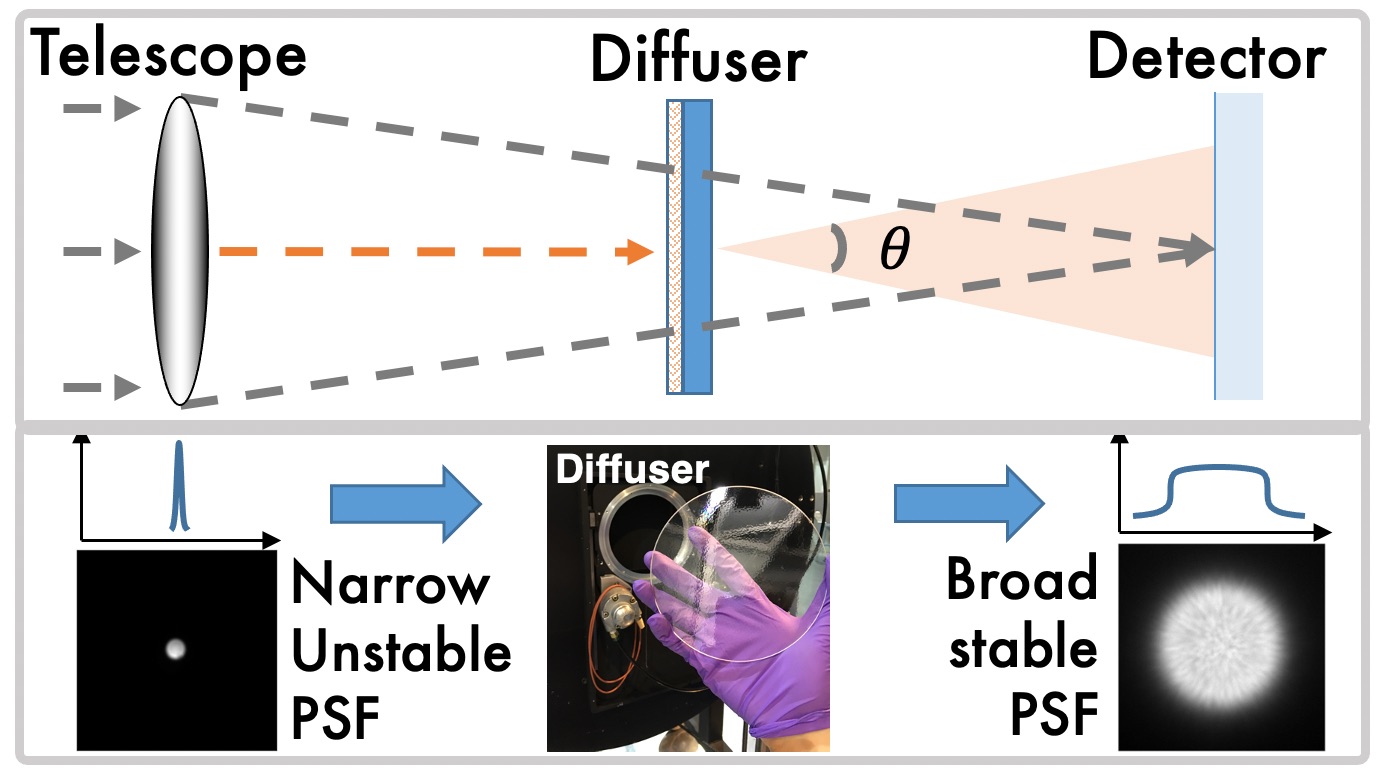
Precision Photometry with Engineered Diffusers
Precision ground-based photometric facilities play a critical role in confirming and characterizing transiting exoplanet candidates from space-based surveys such as the Transiting Exoplanet Survey Satellite (TESS). In Stefansson et al. 2017, I led the design and implementation of an Engineered Diffuser for the ARCTIC instrument on the 3.5m Telescope at Apache Point Observatory. Produced using specialized nanofabrication techniques, Engineered Diffusers are micro-structured optical devices capable of molding the image of a star into a broad and stable top-hat shape, minimizing photometric errors due to detector, seeing, and scintillation effects. Using the Engineered Diffuser on the 3.5m Telescope, we have demonstrated some of the highest photometric precisions achieved from the ground, or 62ppm precision in 30 minute bins.
As Engineered Diffusers are inexpensive, diffusers have now been installed and used at a number of different observatories to characterize a number of transiting planets (see Observation section below). If you are interested in trying a diffuser on your telescope, check out my Python package iDiffuse, and/or don't hesitate to send me an email.
Relevant Papers:
- Stefansson et al. 2017: Toward Space-like Photometric Precision from the Ground with Beam-shaping Diffusers
- Stefansson et al. 2018b: Extreme precision photometry from the ground with beam-shaping diffusers for K2, TESS, and beyond
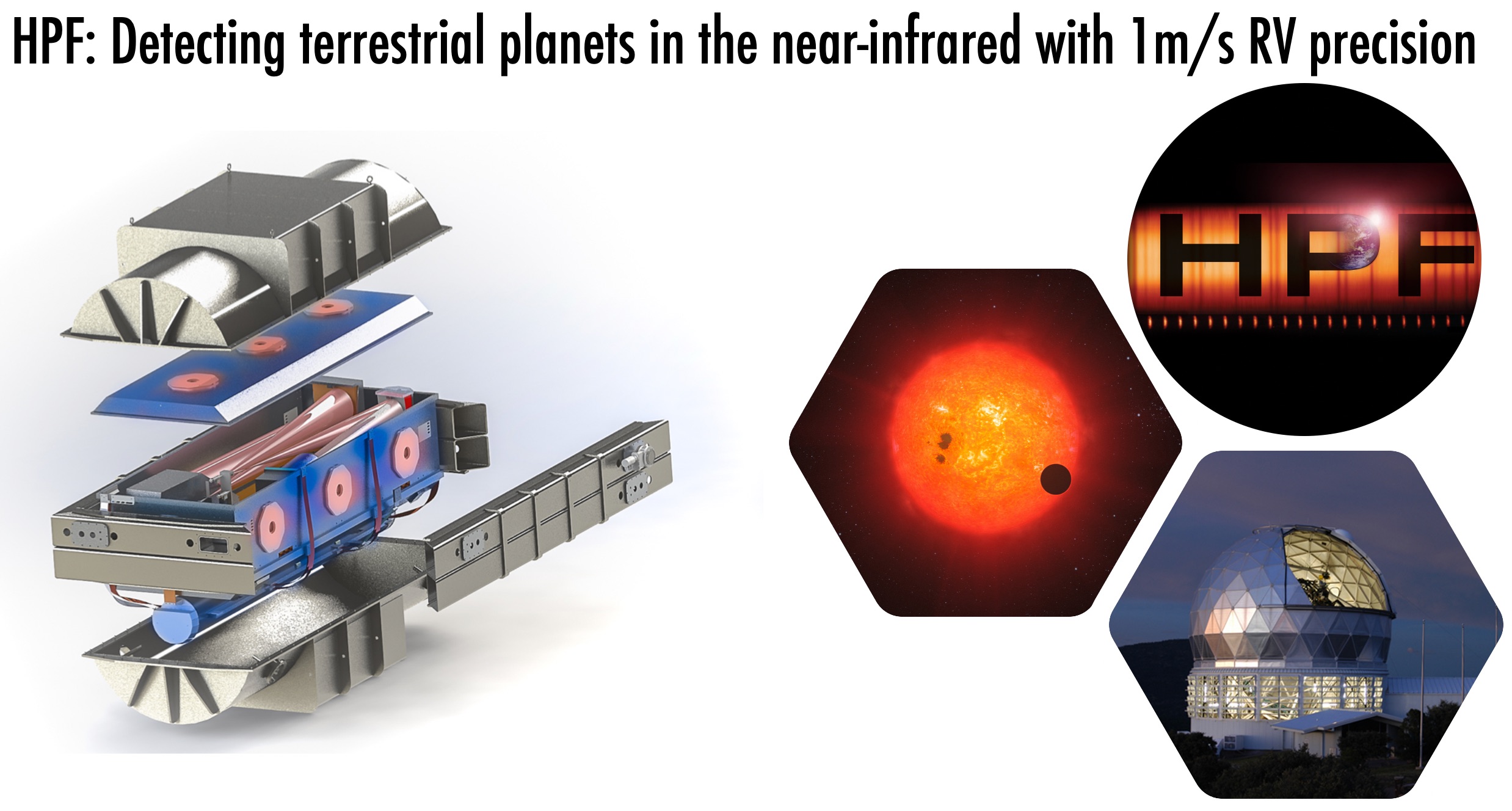
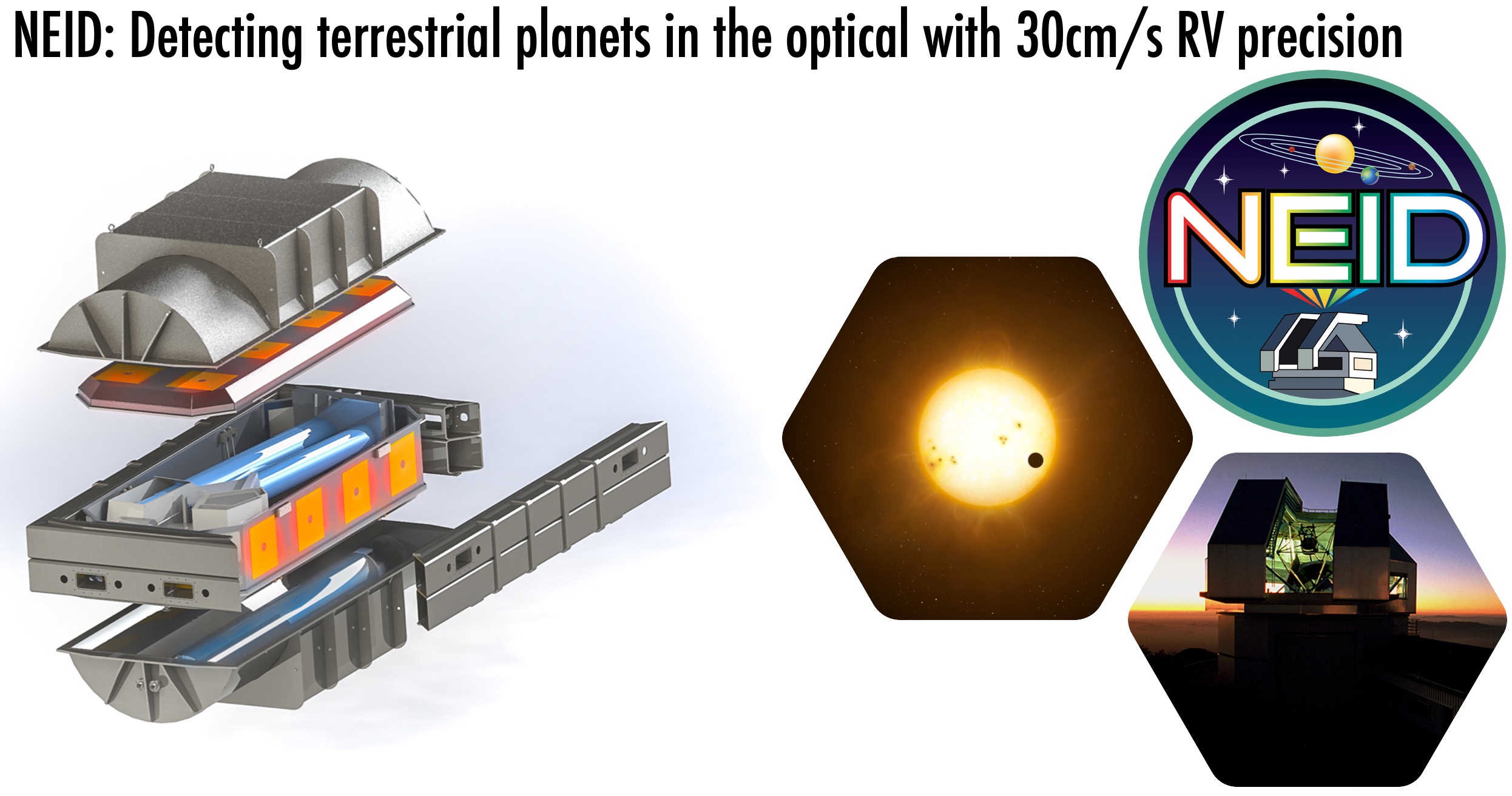
Precision Radial Velocities in the Near Infrared and Optical
I am a part of the instrument and science teams of two next-generation precision radial velocity (RV) spectrographs designed to detect and characterize planets in the habitable-zones around nearby stars: the near-infrared (NIR) Habitable-zone Planet Finder (HPF) on the 10m Hobby-Eberly Telescope, and the NASA/NSF funded NEID Spectrograph for the 3.5m WIYN Telescope at Kitt Peak Observatory.
The main science goal of HPF is to carry out a 5-year survey to detect and characterize terrestrial planets in the Habitable-zone around nearby mid-to-late M-dwarf stars within ~15pc. I currently maintain the HPF RV extractions, where we have demonstrated that HPF is capable of 1.53m/s RV precision on the nearby bright M-dwarf Barnard's Star (Metcalf et al. 2019), the highest precision RVs in the NIR. The main science goal of NEID is to detect and characterize terrestrial planets in the habitable-zone around nearby FGK stars with a goal RV precision of 30cm/s.
For newer updates, check out the HPF blog and the NEID blog.
Relevant Papers:
- Stefansson et al. 2016: A Versatile Technique to Enable Sub-milli-Kelvin Instrument Stability for Precise Radial Velocity Measurements: Tests with the Habitable-zone Planet Finder
- Robertson, Anderson, Stefansson et al. 2019: Ultrastable environment control for the NEID spectrometer: design and performance demonstration
- Metcalf et al. 2019: Stellar spectroscopy in the near-infrared with a laser frequency comb
Press Releases
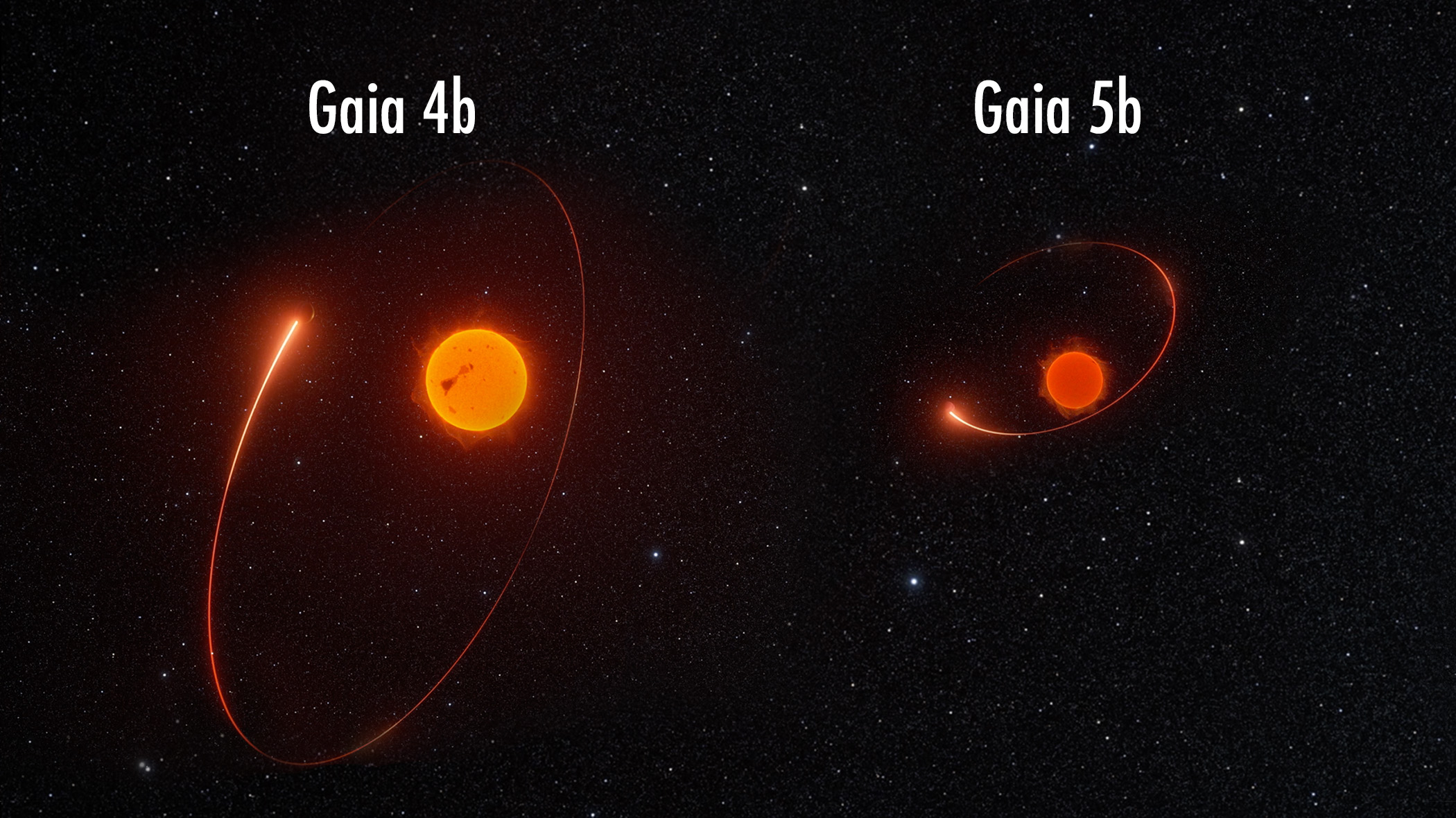
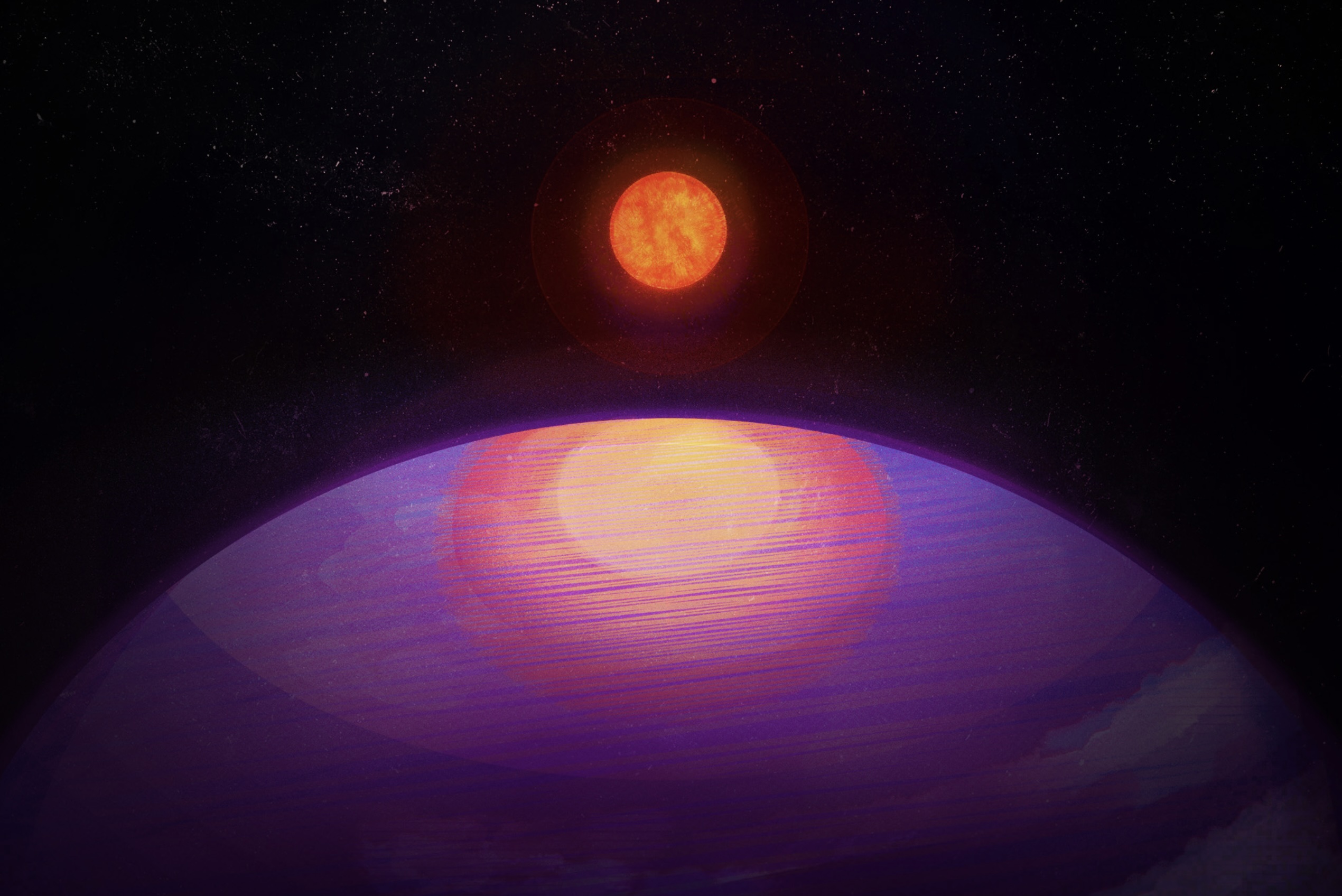
Massive planet too big for its own sun pushes astronomers to rethink exoplanet formation
Discovery of LHS 3154b, a Neptune around an ultracool star (Stefansson+2023, Science).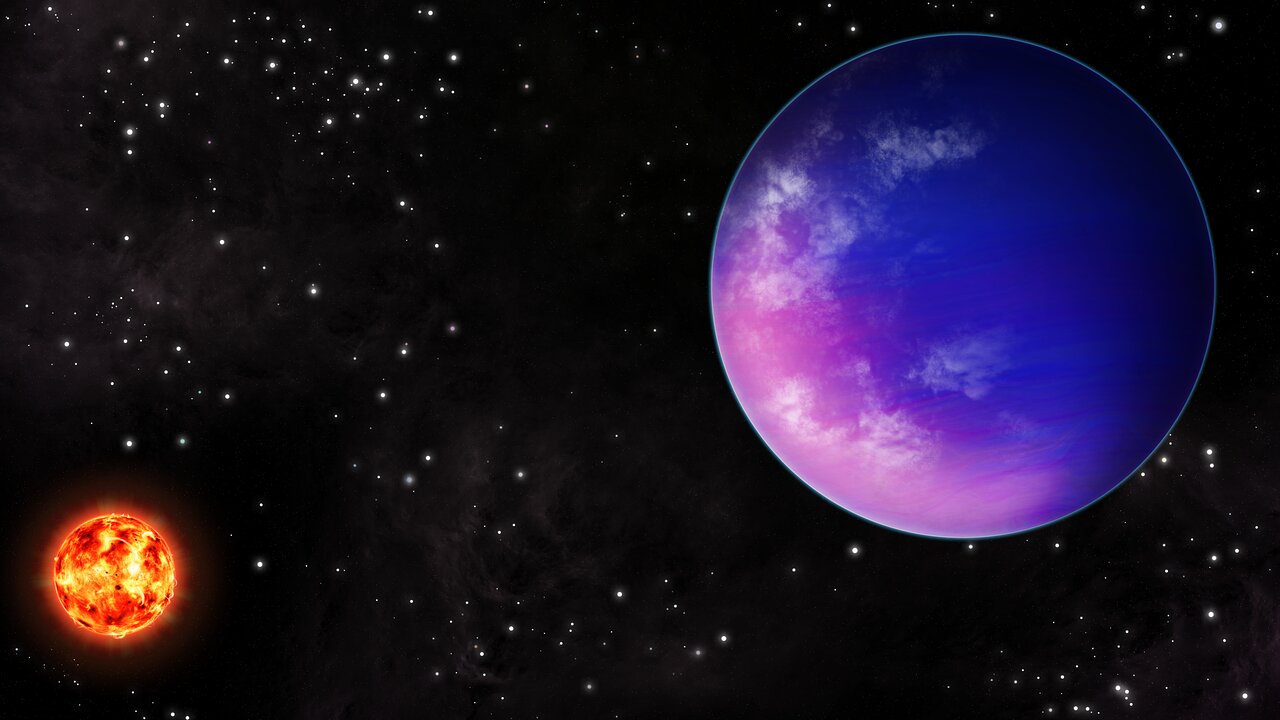
Surprisingly Dense Exoplanet Challenges Planet Formation Theories
The Young Neptune K2-25b is Dense, Eccentric, and Well-Aligned (Stefansson+2020b, AJ)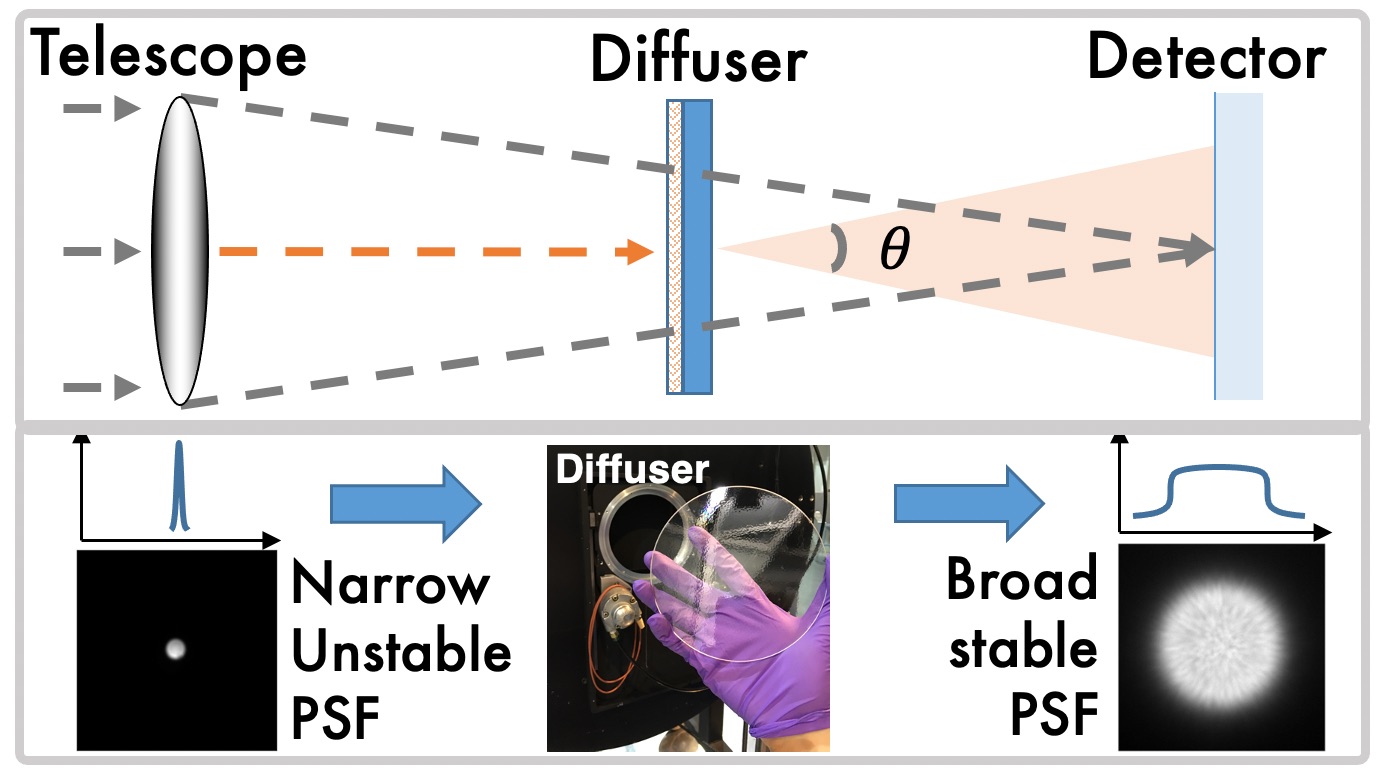
You Can See That From Here
Nanofabricated Engineered Diffusers Enable some of the Highest Precision Photometry from the Ground (Stefansson+2017, ApJ).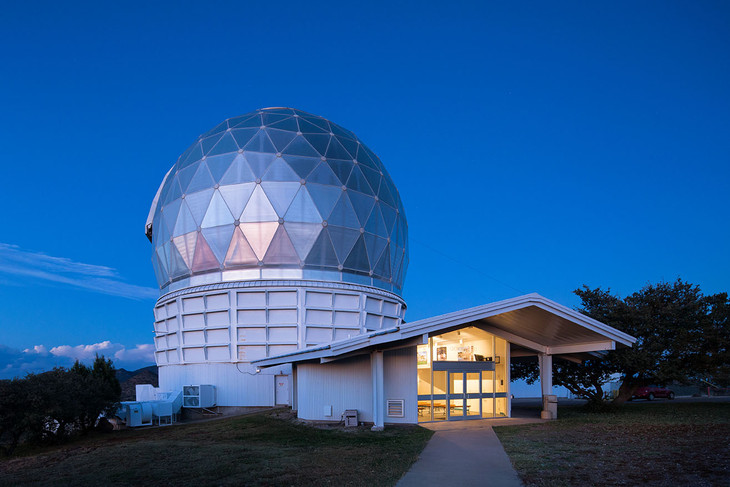
Sub-Neptune-sized Planet Validated with the Habitable-zone Planet Finder
First HPF Planet Validation: a Nearby M-dwarf Star Ideal for Transmission Spectroscopy (Stefansson+2020a, AJ).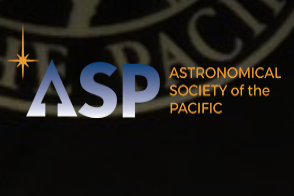
Robert J Trumpler Award 2020
For a PhD Thesis Considered Unusually Important for Astronomy.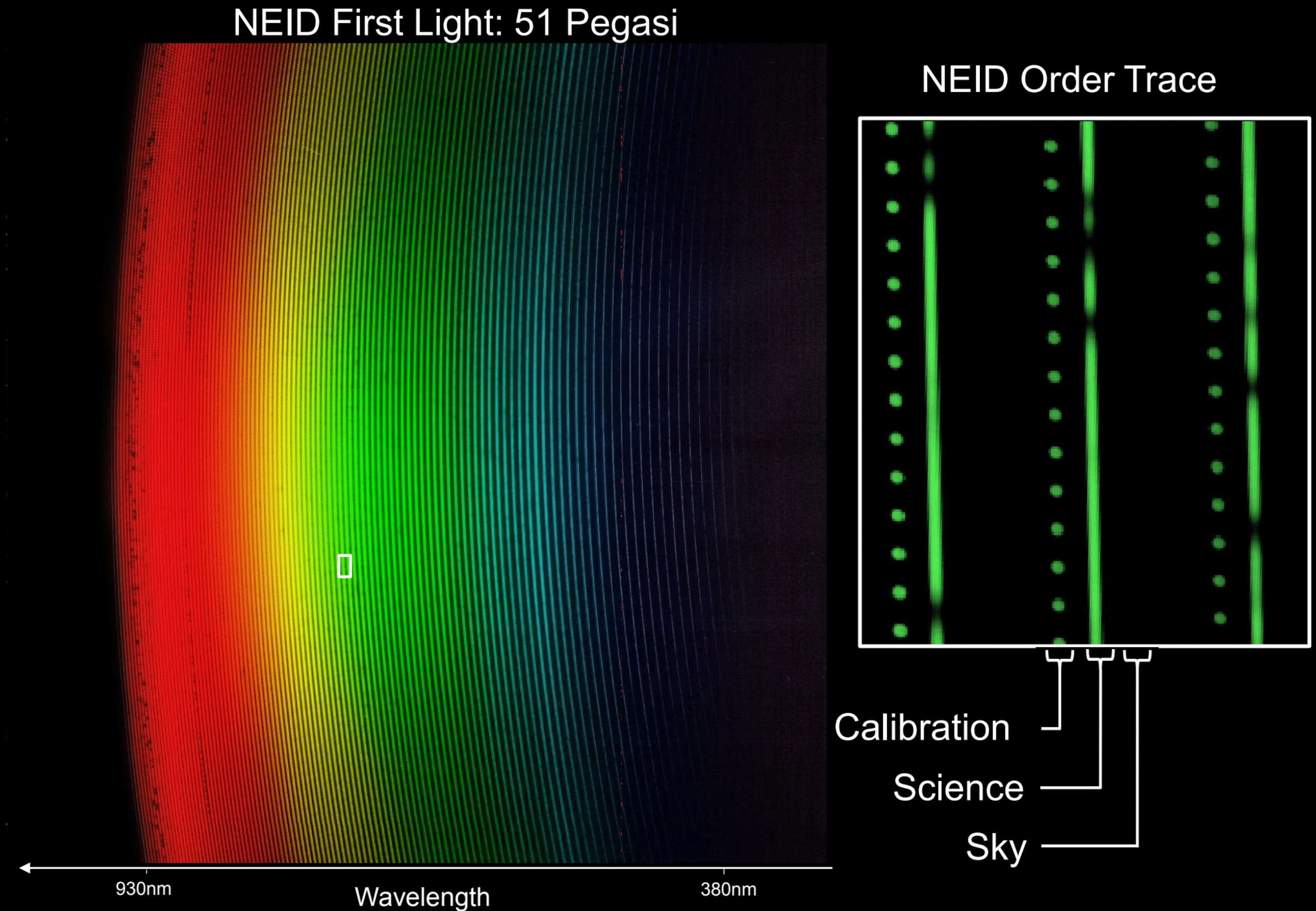
NEID Exoplanet Instrument Sees First Light
NEID, the Precision Doppler Spectrograph for the 3.5m WIYN Telescope, Sees First Light.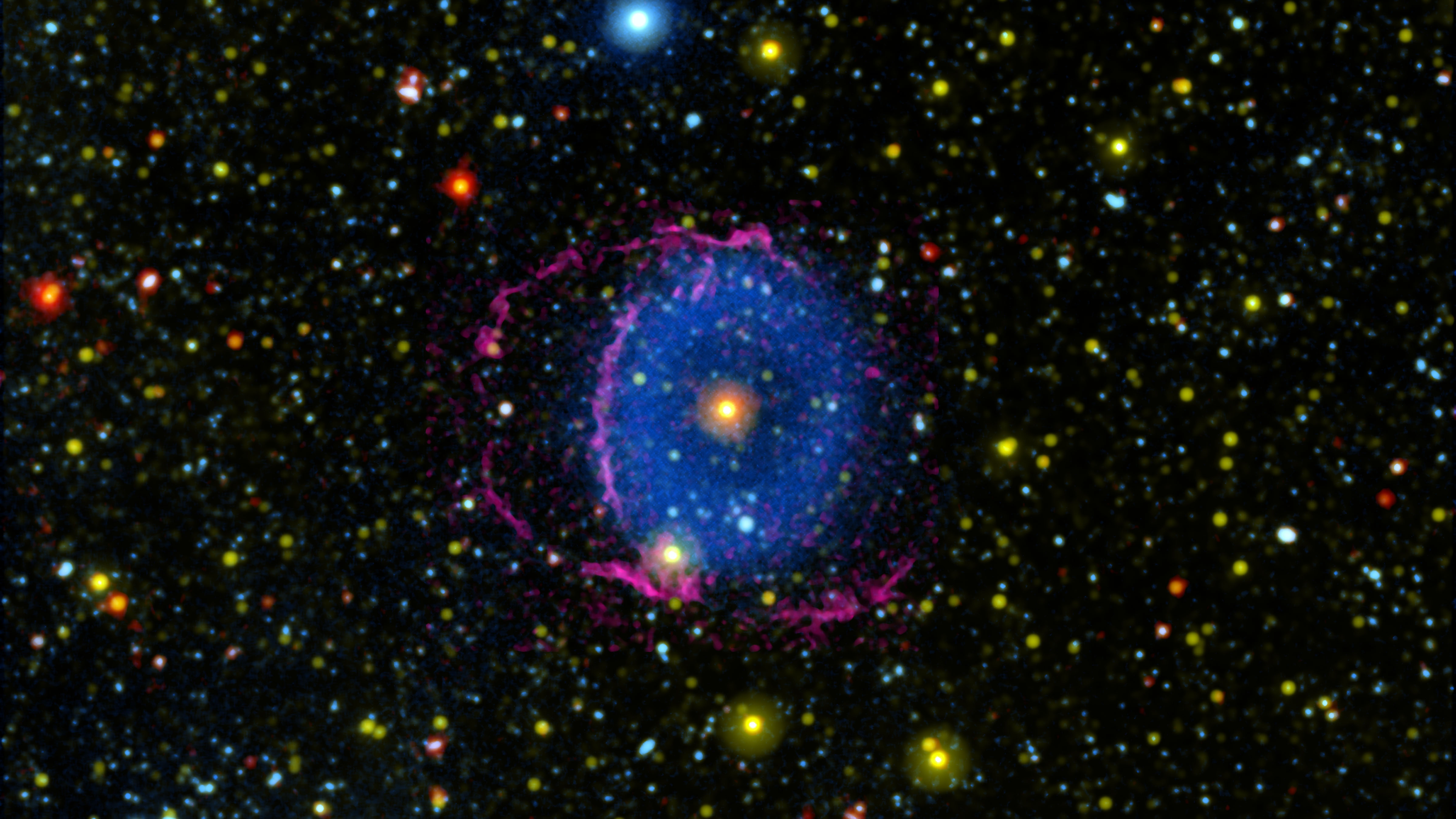
In the mysterious Blue Ring Nebula, scientists see the fate of binary stars
Solving the 16-Year-Old Cosmic Mystery of the Blue Ring Nebula (Hoadley+2020, Nature)Videos
Recent Talks
Outreach
Publications
146 Total, 1 in Science, 3 in Nature.First Author
12 Stefansson, et al. 2025, “Gaia-4b and 5b: Radial Velocity Confirmation of Gaia Astrometric Orbital Solutions Reveal a Massive Planet and a Brown Dwarf Orbiting Low-mass Stars“. AJ, 169, 107arxiv: 2410.05654
11 Stefansson, et al. 2023, “A Neptune-mass exoplanet in close orbit around a very low-mass star challenges formation models“. Science, 382, 1031 arxiv: 2303.13321
10 Stefansson, et al. 2022, “The Warm Neptune GJ 3470b has a Polar Orbit“. ApJL, 931, 15 arxiv: 2111.01295
9 Stefansson, et al. 2020, “A Mini-Neptune and a Radius-Valley-Planet Orbiting the Nearby M2 dwarf TOI-1266 in its Venus-Zone: Validation with the Habitable-zone Planet Finder“. In AJ: 160, 6 (Nov, 2020). arxiv: 2006.11180.
8 Stefansson, et al. 2020, “The Habitable-zone Planet Finder Reveals A High Mass and a Low Obliquity for the Young Neptune K2-25b“, In: AJ 160, 192 (Oct, 2020). arxiv: 2007.12766.
7 Stefansson, et al. 2020, “A sub-Neptune sized planet transiting the M2.5-dwarf G 9-40: Validation with the Habitable-zone Planet Finder“, In: AJ, 159, 100 (March 2020). arxiv: 1912.00291.
6 Stefansson, et al. 2018, “Diffuser-assisted Photometric Follow-up Observations of the Neptune-sized Planets K2-28b and K2-100b”. In: AJ 156, 266 (July 2018). arXiv: 1807.04420.
5 Stefansson, et al. 2018, “Extreme precision photometry from the ground with beam-shaping diffusers for K2, TESS, and beyond”. In: SPIE Conference Series. Vol. 10702. SPIE. Aug. 2018, p. 10702.
4 Stefansson, et al. 2017, “Toward Space-like Photometric Precision from the Ground with Beam-shaping Diffusers”. In: ApJ 848, 9 (Oct. 2017), p. 9. arXiv: 1710.01790.
3 Stefansson, et al. 2016, “A Versatile Technique to Enable Sub-milli-Kelvin Instrument Stability for Precise Radial Velocity Measurements: Tests with the Habitable-zone Planet Finder”. In: ApJ 833, 175 (Dec. 2016), p. 175. arXiv: 1610.06216.
2 Stefansson, et al. 2016, “Ultra-stable temperature and pressure control for the Habitable-zone Planet Finder spectrograph”. In: SPIE Conference Series. Vol. 9908. SPIE. Aug. 2016, p. 990871.
1 Stefansson, et al. 2011, "Samþætting vökvarása og ljósrása á örflögum (English: "Fabrication of integrated optical and microfluidic devices)" In: Raust (2011).
2nd & 3rd Author
24 Yee, Stefánsson et al. 2025, "The Super-Puff WASP-193b is On A Well-Aligned Orbit". Accepted in AJ, arxiv: https://arxiv.org/abs/2502.17610.
23 Brady, Bean Stefánsson et al. 2024, "A Small Brown Dwarf in an Aligned Orbit around a Young, Fully-Convective M Star.". Accepted in AJ, arxiv: 2411.10402.
22 Espinoza-Retamal, Stefánsson et al. 2024, "HATS-38 b and WASP-139 b join a growing group of hot Neptunes on polar orbits". Accepted in AJ, arxiv: 2406.18631.
21 Fitzmaurice, Stefánsson et al. 2023, "Astrometry and Precise Radial Velocities Yield a Complete Orbital Solution for the Nearby Eccentric Brown Dwarf LHS 1610 b". AJ, 168, 140, arxiv: 2310.07827.
20 Jones, Stefánsson et al. 2023, "TOI-2015b: A Warm Neptune with Transit Timing Variations Orbiting an Active mid M Dwarf". AJ, 168, 93, arxiv: 2310.11775.
19 Frazier, Stefánsson et al. 2023, "NEID Reveals that The Young Warm Neptune TOI-2076b Har a Low Obliquity". ApJL, 944, 41. arxiv: 2212.06266.
18 Harman, Kopparapu, Stefánsson et al. 2021, "A Snowball in Hell: The Potential Steam Atmosphere of TOI-1266c". PSJ, 3, 45. arxiv: 2109.10838.
17 S. Vissapragada, G. Stefánsson, M. Greklek-McKeon et al. 2021, "A Search for Planetary Metastable Helium Absorption in the V1298 Tau System". In: AJ (accepted), (July, 2021). arxiv: 2108.05358.
16 S. Kanodia, G. Stefánsson, C. Cañas et al. 2021, "TOI-532b: The Habitable-zone Planet Finder confirms a Large Super Neptune in the Neptune Desert orbiting a metal-rich M dwarf host". In: AJ (accepted), (July, 2021). arxiv: 2107.13670.
15 V. Krishnamurthy, T. Hirano, G. Stefánsson et al. 2021, "Non-detection of Helium in the upper atmospheres of TRAPPIST-1b, e and f". In: AJ (accepted), (May, 2021). arxiv: 2106.11444.
14 J. Lubin, P. Robertson, G. Stefansson et al. 2021, "Stellar Activity Manifesting at a One Year Alias Explains Barnard b as a False Positive". In: AJ (accepted), (May, 2021). arxiv: 2105.07005.
13 S. Mahadevan, G. Stefánsson, P. Robertson et al. 2021, "The Habitable-zone Planet Finder Detects a Terrestrial-mass Planet Candidate Closely Orbiting Gliese 1151: The Likely Source of Coherent Low-frequency Radio Emission from an Inactive Star". In: ApJL (accepted), (Feb, 2021). arxiv: 2102.02233.
12 C. Cañas, G. Stefansson, S. Kanodia, et al. 2020, "A warm Jupiter transiting an M dwarf: A TESS single transit event confirmed with the Habitable-zone Planet Finder". In: AJ, 160, 147 arXiv: 2007.07098.
11 S. Kanodia, C. Cañas, G. Stefansson et al. 2020, "TOI-1728b: The Habitable-zone Planet Finder confirms a warm super Neptune orbiting an M dwarf host". In: ApJ, 899, 29 (Aug, 2020). arXiv: 2006.14546.
10 P. Robertson, G. Stefansson, Suvrath Mahadevan, et al. 2020, "Persistent starspot signals on M dwarfs: multi-wavelength Doppler observations with the Habitable-zone Planet Finder and Keck/HIRES". In: ApJ, 897, 125 (July 2020). arXiv: 2005.09657.
9 J. Ninan, G. Stefansson, S. Mahadevan, et al. 2020, "Evidence for He I 10830 A absorption during the transit of a warm Neptune around the M-dwarf GJ 3470 with the Habitable-zone Planet Finder". In: ApJ, 894, 97 (May 2020). arXiv: 1910.02070.
8 J. Ninan, S. Mahadevan, G. Stefansson et al. 2019, "Impact of crosshatch patterns in H2RGs on high precision radial velocity measurements: Exploration of measurement and mitigation paths with HPF". In: Accepted for Publication in ISPA 2018 (2019). arXiv: 1903.06614.
7 S. Kanodia, A. Wolfgang, G. Stefansson, et al. 2019, "Mass-Radius relationship for M dwarf exoplanets: Comparing nonparametric and parametric methods". In: ApJ 882, 38 (Sep. 2019), p. 14. arXiv: 1903.00042.
6 C. von Essen, G. Stefansson, M. Mallonn, et al. 2019, "First Light of Engineered Diffusers at the Nordic Optical Telescope Reveal Time Variability in the Optical Eclipse Depth of WASP-12b". In: A&A, 628, 11 (August 2019). arXiv: 1904.05362
5 C. Cañas, G. Stefansson, A. J. Monson, et al. 2019, "TOI-150: A transiting hot Jupiter in the TESS southern CVZ". In: ApJL 877, 29 (June 2019), p. 8. arXiv: 1902.09710.
4 P. Robertson, T. Anderson, G. Stefansson, et al. 2019, “Ultrastable environment control for the NEID spectrometer: design and performance demonstration”. In: JATIS, 015003 (Jan 2019). arXiv: 1902.07729.
3 Y. Li, Stefansson, G., P. Robertson, et al. 2017, “A Candidate Transit Event around Proxima Centauri”. In: Research Notes of the American Astronomical Society 1, 49 (Dec. 2017), p. 49. arXiv: 1712.04483.
2 C. Bender, P. Robertson, Stefansson, G. et al. 2016, “The instrument control software package for the Habitable-Zone Planet Finder spectrometer”. In: SPIE Conference Series. Vol. 9913. SPIE. Aug. 2016, p. 991338.
1 Slovinsky, I., Stefansson, G., Kossoy A., et al. 2013, “Propagation Loss of Long-Range Surface Plasmon Polariton Gold Stripe Waveguides in the Thin-Film Limit”. In: Plasmonics 8.4 (2013), pp. 1613–1619.
Coauthor
110Quang H. Tran, Brendan P. Bowler, William D. Cochran, Chad F. Bender, Samuel Halverson, Suvrath Mahadevan, Joe P. Ninan, Paul Robertson, Arpita Roy, Guðmundur Stefánsson, Ryan C. Terrien. "The Epoch of Giant Planet Migration Planet Search Program. III. The Occurrence Rate of Young Giant Planets Inside the Water Ice Line". AJ (accepted), arxiv: 2506.08078.
109Mark R. Giovinazzi, Cullen H. Blake, Paul Robertson, Andrea S.J. Lin, Arvind F. Gupta, Suvrath Mahadevan, Rachel B. Fernandes, Jason T. Wright, Daniella Bardalez Gagliuffi, Jiayin Dong, Evan Fitzmaurice, Samuel Halverson, Shubham Kanodia, Sarah E. Logsdon, Jacob K. Luhn, Michael W. McElwain, Andy Monson, Joe P. Ninan, Jayadev Rajagopal, Arpita Roy, Christian Schwab, Gudmundur Stefánsson, Ryan Terrien, Jason D. Eastman, Jonathan Horner, Peter Plavchan, Sharon X. Wang, Maurice L. Wilson, Robert A. Wittenmyer. "The NEID Earth Twin Survey. II. Dynamical Masses in Seven High-acceleration Star Systems". AJ (accepted), arxiv: 2505.12563.
108Rachel B Fernandes, Shubham Kanodia, Megan Delamer, Andrew Hotnisky, Te Han, Caleb I Canas, Jessica Libby-Roberts, Varghese Reji, Arvind F Gupta, Jaime A Alvarado-Montes, Chad F Bender, Cullen H Blake, William D Cochran, Zoe L de Beurs, Scott A Diddams, Jiayin Dong, Mark E Everett, Eric B Ford, Samuel Halverson, Jesus Higuera, Henry A Kobulnicky, Daniel M Krolikowski, Alexander Larsen, Andrea SJ Lin, Suvrath Mahadevan, Michael W McElwain, Andrew Monson, Joe P Ninan, Leonardo A Paredes, Yatrik G Patel, Paul Robertson, Gabrielle Ross, Arpita Roy, Christian Schwab, Gudmundur Stefansson, Daniel J Stevens, Andrew M Vanderburg, Jason Wright. "Searching for GEMS: Confirmation of TOI-5573b, a Cool, Saturn-like Planet Orbiting An M-dwarf". AJ (accepted), arxiv: 2505.08947.
107Patrick Tamburo, Samuel W. Yee, Juliana García-Mejía, Gudmundur Stefánsson, David Charbonneau, Allyson Bieryla, Andrew W. Howard, Howard Isaacson, Benjamin J. Fulton, Aaron Householder. "The True Stellar Obliquity of a Sub-Saturn Planet from the Tierras Observatory and KPF". AJ (accepted), arxiv: 2505.03628.
106Gavin Wang, William O. Balmer, Laurent Pueyo, Daniel Thorngren, Stephen P. Schmidt, Le-Chris Wang, Kevin C. Schlaufman, Guðmundur Stefánsson, Zafar Rustamkulov, David K. Sing. "A Revised Density Estimate for the Largest Known Exoplanet, HAT-P-67 b". AJ, 169, 336, arxiv: 2504.13997.
105Te Han, Paul Robertson, Caleb I. Cañas, Gudmundur Stefansson, Shubham Kanodia, Joe P. Ninan, Jaime A. Alvarado-Montes, Chad F. Bender, Jiayin Dong, Rachel Fernandes, Arvind F. Gupta, Samuel Halverson, Daniel M. Krolikowski, Andrea S.J. Lin, Suvrath Mahadevan, Leonardo A. Paredes, Arpita Roy, Christian Schwab, Ryan C. Terrien. "NEIDSpecMatch: stellar parameter estimation with NEID spectra using an empirical library". RNAAS, 9 63. arxiv: 2503.16729.
104Ritvik Basant, Rafael Luque, Jacob L. Bean, Andreas Seifahrt, Madison Brady, Lily L. Zhao, Nina Brown, Tanya Das, Julian Stürmer, David Kasper, Rohan Gupta, Guðmundur Stefánsson. "Four sub-Earth planets orbiting Barnard's Star from MAROON-X and ESPRESSO". ApJL, 982, 1, arxiv: 2503.08095.
103Rena A. Lee, Fei Dai, Andrew W. Howard, Samuel Halverson, Jonathan Gomez Barrientos, Michael Greklek-McKeon, Heather A. Knutson, Benjamin J. Fulton, Guðmundur Stefánsson, Jack Lubin, Howard Isaacson, Casey L. Brinkman, Nicholas Saunders, Daniel Hey, Daniel Huber, Lauren M. Weiss, Leslie A. Rogers, Diana Valencia, Mykhaylo Plotnykov, Kimberly Paragas, Renyu Hu, Te Han, Erik A. Petigura, Ryan Rubenzahl, David R. Ciardi, Aaron Householder, Gregory J. Gilbert, J. M. Joel Ong, Jingwen Zhang, Jacob Luhn, Luke Handley, Corey Beard, Steven Giacalone, Rae Holcomb, Judah Van Zandt, Ashley D. Baker, Max Brodheim, Matt Brown, David Charbonneau, Karen A. Collins, Ian J. M. Crossfield, William Deich, Xavier Dumusque, Steven R. Gibson, Emily Gilbert, Grant M. Hill, Bradford Holden, Jon M. Jenkins, Stephen Kaye, Russ R. Laher, Kyle Lanclos, W. Garrett Levine, Joel Payne, Alex S. Polanski, John O'Meara, George R. Ricker, Kodi Rider, Paul Robertson, Arpita Roy, Joshua E. Schlieder, Christian Schwab, Sara Seager, Abby P. Shaum, Martin M. Sirk, Stephanie Striegel, Johanna Teske, John Valliant, Roland Vanderspek, Gautam Vasisht, Josh Walawender, Sharon Xuesong Wang, Joshua N. Winn, Edward Wishnow, Sherry Yeh. "TOI-6324b: An Earth-Mass Ultra-Short-Period Planet Transiting a Nearby M Dwarf.". AJ (submitted), arxiv: 2502.16087.
102Ritvik Basant, Tanya Das, Jacob L. Bean, Rafael Luque, Andreas Seifahrt, Madison Brady, Nina Brown, Julian Stürmer, David Kasper, Guðmundur Stefánsson. "Calibrating the Instrumental Drift in MAROON-X using an Ensemble Analysis". AJ (accepted), arxiv: 2502.15074.
101K. Barkaoui, J. Korth, E. Gaidos, E. Agol, H. Parviainen, F.J. Pozuelos, E. Palle, N. Narita, S. Grimm, M. Brady, J.L. Bean, G. Morello, B.V. Rackham, A.J. Burgasser, V. Van Grootel, B. Rojas-Ayala, A. Seifahrt, E. Marfil, V.M. Passegger, M. Stalport, M. Gillon, K.A. Collins, A. Shporer, S. Giacalone, S. Yalçınkaya, E. Ducrot, M. Timmermans, A.H.M.J. Triaud, J. de Wit, A. Soubkiou, C.N. Watkins, C. Aganze, R. Alonso, P.J. Amado, R. Basant, Ö. Bastürk, Z. Benkhaldoun, A. Burdanov, Y. Calatayud-Borras, J. Chouqar, D.M. Conti, K.I. Collins, F. Davoudi, L. Delrez, C.D. Dressing, J. de Leon, M. D'evora-Pajares, B.O. Demory, G. Dransfield, E. Esparza-Borges, G. Fern'andez-Rodriguez, I. Fukuda, A. Fukui, P.P.M. Gallardo, L. Garcia, N.A. Garcia, M. Ghachoui, S. Gerald'ia-González, Y. Gómez Maqueo Chew, J. González-Rodríguez, M.N. Günther, Y. Hayashi, K. Horne, M.J. Hooton, C.C. Hsu, K. Ikuta, K. Isogai, E. Jehin, J.M. Jenkins, K. Kawauchi, T. Kagetani, Y. Kawai, D. Kasper, J.F. Kielkopf, P. Klagyivik, G. Lacedelli, D.W. Latham, F. Libotte, R. Luque, J.H. Livingston, L. Mancini, B. Massey, M. Mori, S. Muñoz Torres, F. Murgas, P. Niraula, J. Orell-Miquel, David Rapetti, R. Rebolo-Lopez, G. Ricker, R. Papini, P.P. Pedersen, A. Peláez-Torres, J.A. Pérez-Prieto, E. Poultourtzidis, P.M. Rodriguez, D. Queloz, A.B. Savel, N. Schanche, M. Sanchez-Benavente , L. Sibbald, R. Sefako, S. Sohy, A. Sota, R.P. Schwarz, S. Seager, D. Sebastian, J. Southworth, M. Stangret, G. Stefánsson, J. Stürmer, G. Srdoc, S.J. Thompson, Y. Terada, R. Vanderspek, G. Wang, N. Watanabe, F.P. Wilkin, J. Winn, R.D. Wells, C. Ziegler, S. Zúñiga-Fernández. "TOI-2015b: a sub-Neptune in strong gravitational interaction with an outer non-transiting planet". A&A (accepted), arxiv: 2502.07074.
100Caleb I. Cañas, Jacob Lustig-Yaeger, Shang-Min Tsai, Simon Müller, Ravit Helled, Dana R. Louie, Giannina Guzmán Caloca, Shubham Kanodia, Peter Gao, Jessica Libby-Roberts, Kevin K. Hardegree-Ullman, Knicole D. Colón, Ian Czekala, Megan Delamer, Te Han, Andrea S.J. Lin, Suvrath Mahadevan, Erin M. May, Joe P. Ninan, Anjali A. A. Piette, Guðmundur Stefánsson, Kevin B. Stevenson, Johanna Teske, Nicole L. Wallack. "GEMS JWST: Transmission spectroscopy of TOI-5205b reveals significant stellar contamination and a metal-poor atmosphere.". AJ (submitted), arxiv: 2502.06966.
99Alexander Larsen, Tera N. Swaby, Henry A. Kobulnicky, Caleb I. Canas, Shubham Kanodia, Jessica Libby-Roberts, Andrew Monson, Arvind Gupta, William Cochran, Suvrath Mahadevan, Chad Bender, Scott A. Diddams, Samuel Halverson, Andrea S.J. Lin, Maxwell Moe, Joe Ninan, Paul Robertson, Arpita Roy, Christian Schwab, Gudmundur Stefansson "Searching for GEMS: Discovery and Characterization of Two Brown Dwarfs Around M Dwarfs.". AJ (accepted), arxiv: 2501.16554.
98Corey Beard, Paul Robertson, Jack Lubin, Te Han, Rae Holcomb, Pranav Premnath, R. Paul Butler, Paul A. Dalba, Brad Holden, Cullen H. Blake, Scott A. Diddams, Arvind F. Gupta, Samuel Halverson, Daniel M. Krolikowski, Dan Li, Andrea S.J. Lin, Sarah E. Logsdon, Emily Lubar, Suvrath Mahadevan, Michael W. McElwain, Joe P. Ninan, Leonardo A. Paredes, Arpita Roy, Christian Schwab, Gudmundur Stefansson, Ryan C. Terrien, Jason T. Wright. "Jitter Across 15 Years: Leveraging Precise Photometry from Kepler and TESS to Extract Exoplanets from Radial Velocity Time Series.". AJ, 169, 92, arxiv: 2412.11329.
97Juan I. Espinoza-Retamal, Andrés Jordán, Rafael Brahm, Cristobal Petrovich, Elyar Sedaghati, Guðmundur Stefánsson, Melissa J. Hobson, Marcelo Tala Pinto, Diego J. Muñoz, Gavin Boyle, Rodrigo Leiva, Vincent Suc. "The Spin-Orbit Alignment of 8 Warm Gas Giant Systems". AJ, submitted, arxiv: 2412.08692.
96Lauren Doyle, Caleb I. Cañas, Jessica E. Libby-Roberts, Heather M. Cegla, Guðmundur K. Stefánsson, David Anderson, David J. Armstrong, Chad Bender, Daniel Bayliss, Theron W. Carmichael, Sarah Casewell, Shubham Kanodia, Marina Lafarga, Andrea S.J. Lin, Suvrath Mahadevan, Andy Monson, Paul Robertson, Dimitri Veras. "The First Spin-Orbit Obliquity of an M dwarf/brown dwarf System: An eccentric and aligned TOI-2119 b". MNRAS, 536, 4, arxiv: 2411.18567.
95Andrew Hotnisky, Shubham Kanodia, Jessica Libby-Roberts, Suvrath Mahadevan, Caleb I. Canas, Arvind F. Gupta, Te Han, Henry A. Kobulnicky, Alexander Larsen, Paul Robertson, Michael Rodruck, Gudmundur Stefansson, William D. Cochran, Megan Delamer, Scott A. Diddams, Rachel B. Fernandes, Samuel Halverson, Leslie Hebb, Andrea S.J. Lin, Andrew Monson, Joe P. Ninan, Arpita Roy, Christian Schwab. "Searching for GEMS: Two Super-Jupiters Around M Dwarfs that May have Formed via Gravitational Instability". AJ, 170, 1, arxiv: 2411.08159.
94Arvind F. Gupta, Jacob K. Luhn, Jason T. Wright, Suvrath Mahadevan, Paul Robertson, Daniel M. Krolikowski, Eric B. Ford, Caleb I. Cañas, Samuel Halverson, Andrea S.J. Lin, Shubham Kanodia, Evan Fitzmaurice, Christian Gilbertson, Chad F. Bender, Cullen H. Blake, Jiayin Dong, Mark R. Giovinazzi, Sarah E. Logsdon, Andrew Monson, Joe P. Ninan, Jayadev Rajagopal, Arpita Roy, Christian Schwab, Guðmundur Stefánsson. "The NEID Earth Twin Survey. I. Confirmation of a 31-day planet orbiting HD 86728". AJ, 169, 1, arxiv: 2409.12315.
93Lia Marta Bernabò, Shubham Kanodia, Caleb I. Canas, William D. Cochran, Szilárd Csizmadia, Suvrath Mahadevan, Gudhmundur Stefánsson, Arvind F. Gupta, Andrew Monson, Henry A. Kobulnicky, Alexander K. Larsen, Ethan G. Cotter, Alexina Birkholz, Tera N. Swaby, Gregory Zeimann, Chad F. Bender, Scott A. Diddams, Jessica E. Libby-Roberts, Andrea S.J. Lin, Joe P. Ninan, Heike Rauer, Varghese Reji, Paul Robertson, Arpita Roy, Christian Schwab. "Searching for GEMS: TOI-6383Ab, a giant planet transiting an M3-dwarf star in a binary system". AJ, 168, 273, arxiv: 2409.16889.
92Casey L. Brinkman, Lauren M. Weiss, Daniel Huber, Rena A. Lee, Jared Kolecki, Gwyneth Tenn, Jingwen Zhang, Suchitra Narayanan, Alex S. Polanski, Fei Dai, Jacob L. Bean, Corey Beard, Madison Brady, Max Brodheim, Matt Brown, William Deich, Jerry Edelstein, Benjamin J. Fulton, Steven Giacalone, Steven R. Gibson, Gregory J. Gilbert, Samuel Halverson, Luke Handley, Grant M. Hill, Rae Holcomb, Bradford Holden, Aaron Householder, Andrew W. Howard, Howard Isaacson, Stephen Kaye, Russ R. Laher, Kyle Lanclos, J. M. Joel Ong, Joel Payne, Eric A. Petigura, Daria Pidhorodetska, Claire Poppett, Arpita Roy, Ryan Rubenzahl, Nicholas Saunders, Christian Schwab, Andreas Seifahrt, Abby P. Shaum, Martin M. Sirk, Chris Smith, Roger Smith, Guðmundur Stefánsson, Julian Stürmer, Jim Thorne, Emma V. Turtelboom, Dakotah Tyler, John Valliant, Judah Van Zandt, Josh Walawender, Samuel W. Yee, Sherry Yeh, Jon Zink. "The Compositions of Rocky Planets in Close-in Orbits Tend to be Earth-Like". AJ, accepted, arxiv: 2410.00213.
91Kento Masuda, Jessica E. Libby-Roberts, John H. Livingston, Kevin B. Stevenson, Peter Gao, Shreyas Vissapragada, Guangwei Fu, Te Han, Michael Greklek-McKeon, Suvrath Mahadevan, Eric Agol, Aaron Bello-Arufe, Zachory Berta-Thompson, Caleb I. Canas, Yayaati Chachan, Leslie Hebb, Renyu Hu, Yui Kawashima, Heather A. Knutson, Caroline V. Morley, Catriona A. Murray, Kazumasa Ohno, Armen Tokadjian, Xi Zhang, Luis Welbanks, Matthew C. Nixon, Richard Freedman, Norio Narita, Akihiko Fukui, Jerome P. de Leon, Mayuko Mori, Enric Palle, Felipe Murgas, Hannu Parviainen, Emma Esparza-Borges, Daniel Jontof-Hutter, Karen A. Collins, Paul Benni, Khalid Barkaoui, Francisco J. Pozuelos, Michael Gillon, Emmanuel Jehin, Zouhair Benkhaldoun, Suzanne Hawley, Andrea S.J. Lin, Gudmundur Stefansson Allyson Bieryla, Mesut Yilmaz, Hakan Volkan Senavci, Eric Girardin, Giuseppe Marino, Gavin Wang. "A Fourth Planet in the Kepler-51 System Revealed by Transit Timing Variations". AJ, 168, 294, arxiv: 2410.01625.
90Jiayin Dong, Ashley Chontos, George Zhou, Gudmundur Stefansson, Songhu Wang, Chelsea X. Huang, Arvind F. Gupta, Samuel Halverson, Shubham Kanodia, Jacob K. Luhn, Suvrath Mahadevan, Andrew Monson, Jaime A. Alvarado-Montes, Joe P. Ninan, Paul Robertson, Arpita Roy, Christian Schwab, Jason T. Wright. "Origins of Super Jupiters: TOI-2145b Has a Moderately Eccentric and Nearly Aligned Orbit". AJ, 169, 4, arxiv: 2411.01356.
89J. R. Callingham, B. J. S. Pope, R. D. Kavanagh, S. Bellotti, S. Daley-Yates, M. Damasso, J.-M. Grießmeier, M. Güdel, M. Günther, M. M. Kao, B. Klein, S. Mahadevan, J. Morin, J. D. Nichols, R. A. Osten, M. Pérez-Torres, J. S. Pineda, J. Rigney, J. Saur, G. Stefánsson, J. D. Turner, H. Vedantham, A. A. Vidotto, J. Villadsen, P. Zarka. "Radio Signatures of Star-Planet Interactions, Exoplanets, and Space Weather". Nature Astronomy, 8, 1359, arxiv: 2409.15507.
88Jack Lubin, Erik A. Petigura, Judah Van Zandt, Corey Beard, Fei Dai, Samuel Halverson, Rae Holcomb, Andrew W. Howard, Howard Isaacson, Jacob Luhn, Paul Robertson, Ryan A. Rubenzahl, Gudmundur Stefansson, Joshua N. Winn, Max Brodheim, William Deich, Grant M. Hill, Steven R. Gibson, Bradford Holden, Aaron Householder, Russ R. Laher, Kyle Lanclos, Joel Payne, Arpita Roy, Roger Smith, Abby P. Shaum, Christian Schwab, Josh Walawender. "The HD 191939 Exoplanet System is Well-Aligned and Flat". AJ, 168, 196, arxiv: 2409.06795.
87E. Martioli, R.P. Petrucci, E. Jofre, G. Hebrard, L. Ghezzi, Y. Gomez Maqueo Chew, R.F. Diaz, H.D. Perottoni, L.H. Garcia, D. Rapetti, A. Lecavelier des Etangs, L. de Almeida, L. Arnold, E. Artigau, R. Basant, J.L. Bean, A. Bieryla, I. Boisse, X. Bonfils, M. Brady, C. Cadieux, A. Carmona, N.J. Cook, X. Delfosse, J.-F. Donati, R. Doyon, E. Furlan, S.B. Howell, J.M. Jenkins, D. Kasper, F. Kiefer, D.W. Latham, A.M. Levine, D. Lorenzo-Oliveira, R. Luque, K. McLeod, J. Melendez, C. Moutou, Y. Netto, T.A. Pritchard, P. Rowden, A. Seifahrt, G. Stefansson, J. Sturmer, D. J Twicken. "TOI-3568 b: a super-Neptune in the sub-Jovian desert". A&A, 690, 312, arxiv: 2409.03704.
86Varghese Reji, Shubham Kanodia, Joe Ninan, Caleb I. Cañas, Jessica Libby-Roberts, Andrea S.J. Lin, Arvind F Gupta, Tera N. Sewaby, Alexander Larsen, Henry A. Kobulnicky, Philip I. Choi, Nez Evans, Sage Santomenna, Isabelle Winnick, Larry Yu, Jaime A. Alvarado-Montes, Chad Bender, Lia Marta Bernabò, Cullen H. Blake, William D. Cochran, Scott A. Diddams, Samuel Halverson, Te Han, Fred Hearty, Sarah E. Logsdon, Suvrath Mahadevan, Andrew Monson, Michael McElwain, Paul Robertson, Devendra Ojha, Arpita Roy, Christian Schwab, Gudmundur Stefansson, Jason Wright. "Searching for GEMS: TOI-5688 A b, a low-density giant orbiting a high-metallicity early M-dwarf". AJ, 169, 187, arxiv: 2409.01371.
85Christian Gilbertson, Eric B. Ford, Samuel Halverson, Evan Fitzmaurice, Cullen H. Blake, Guðmundur Stefánsson, Suvrath Mahadevan, Jason T. Wright, Jacob K. Luhn, Joe P. Ninan, Paul Robertson, Arpita Roy, Christian Schwab, Ryan C. Terrien."Data-Driven Modeling of Telluric Features and Stellar Variability with StellarSpectraObservationFitting.jl". Submitted to AJ, arxiv: 2408.17289.
84Shubham Kanodia, Arvind F. Gupta, Caleb I. Canas, Lia Marta Bernabo, Varghese Reji, Te Han, Madison Brady, Andreas Seifahrt, William D. Cochran, Nidia Morrell, Ritvik Basant, Jacob Bean, Chad F. Bender, Zoe L. de Beurs, Allyson Bieryla, Alexina Birkholz, Nina Brown, Franklin Chapman, David R. Ciardi, Catherine A. Clark, Ethan G. Cotter, Scott A. Diddams, Samuel Halverson, Suzanne Hawley, Leslie Hebb, Rae Holcomb, Steve B. Howell, Henry A. Kobulnicky, Adam F. Kowalski, Alexander Larsen, Jessica Libby-Roberts, Andrea S.J. Lin, Michael B. Lund, Rafael Luque, Andrew Monson, Joe P. Ninan, Brock A. Parker, Nishka Patel, Michael Rodruck, Gabrielle Ross, Arpita Roy, Christian Schwab, Guðmundur Stefánsson, Aubrie Thoms, Andrew Vanderburg. "Searching for GEMS: Characterizing Six Giant Planets around Cool Dwarfs". AJ, 168, 235. arxiv: 2408.14694.
83Eric B. Ford, Chad F. Bender, Cullen H. Blake, Arvind F. Gupta, Shubham Kanodia, Andrea S.J. Lin, Sarah E. Logsdon, Jacob K. Luhn, Suvrath Mahadevan, Michael L. Palumbo III, Ryan C. Terrien, Jason T. Wright, Jinglin Zhao, Samuel Halverson, Emily Hunting, Paul Robertson, Arpita Roy, Gudmundur Stefansson. "Earths within Reach: Evaluation of Strategies for Mitigating Solar Variability using 3.5 years of NEID Sun-as-a-Star Observations". Submitted to AAS, arxiv: 2408.13318.
82I. de Ruiter, K.M. Rajwade, C.G. Bassa, A. Rowlinson, R.A.M.J. Wijers, C.D. Kilpatrick, G. Stefansson, J.R. Callingham, J.W.T. Hessels, T.E. Clarke, W. Peters, R.A.D. Wijnands, T.W. Shimwell, S. ter Veen, V. Morello, G.R. Zeimann, S. Mahadevan. "A white dwarf binary showing sporadic radio pulses at the orbital period". Nature Astronomy, 65, arxiv: 2408.11536.
81Jared C. Siegel, Samuel Halverson, Jacob K. Luhn, Lily L. Zhao, Khaled Al Moulla, Paul Robertson, Chad F. Bender, Ryan C. Terrien, Arpita Roy, Suvrath Mahadevan, Fred Hearty, Joe P. Ninan, Jason T. Wright, Eric B. Ford, Christian Schwab, Guðmundur Stefánsson, Cullen H. Blake, Michael W. McElwain. "Quiet Please: Detrending Radial Velocity Variations from Stellar Activity with a Physically Motivated Spot Model". AJ, 168, 158, arxiv: 2408.07121.
80Corey Beard, Paul Robertson, Mark R. Giovinazzi, Joseph M. Akana Murphy, Eric B. Ford, Samuel Halverson, Te Han, Rae Holcomb, Jack Lubin, Rafael Luque, Pranav Premnath, Chad F. Bender, Cullen H. Blake, Qian Gong, Howard Isaacson, Shubham Kanodia, Dan Li, Andrea S.J. Lin, 5 Sarah E. Logsdon, Emily Lubar, Michael W. McElwain, Andrew Monson, Joe P. Ninan, Jayadev Rajagopal, Arpita Roy, Christian Schwab, Gudmundur Stefansson, Ryan C. Terrien, Jason T. Wright. "Utilizing Photometry from Multiple Sources to Mitigate Stellar Variability in Precise Radial Velocities: A Case Study of Kepler-21". Accepted in AJ, arxiv: 2408.02873.
79Arvind F. Gupta, Sarah C. Millholland, Haedam Im, Jiayin Dong, Jonathan M. Jackson, Ilaria Carleo, Jessica Libby-Roberts, Megan Delamer, Mark R. Giovinazzi, Andrea S. J. Lin, Shubham Kanodia, Xian-Yu Wang, Keivan Stassun, Thomas Masseron, Diana Dragomir, Suvrath Mahadevan, Jason Wright, Jaime A. Alvarado-Montes, Chad Bender, Cullen H. Blake, Douglas Caldwell, Caleb I. Cañas, William D. Cochran, Paul Dalba, Mark E. Everett, Pipa Fernandez, Eli Golub, Bruno Guillet, Samuel Halverson, Leslie Hebb, Jesus Higuera, Chelsea X. Huang, Jessica Klusmeyer, Rachel Knight, Liouba Leroux, Sarah E. Logsdon, Margaret Loose, Michael W. McElwain, Andrew Monson, Joe P. Ninan, Grzegorz Nowak, Enric Palle, Yatrik Patel, Joshua Pepper, Michael Primm, Jayadev Rajagopal, Paul Robertson, Arpita Roy, Donald P. Schneider, Christian Schwab, Heidi Schweiker, Lauren Sgro, Masao Shimizu (清水正雄), Georges Simard, Guðmundur Stefánsson, Daniel J. Stevens, Steven Villanueva, John Wisniewski, Stefan Will, Carl Ziegler."A hot-Jupiter progenitor on a super-eccentric retrograde orbit". Nature, 632, 50.
78Ryan A. Rubenzahl, Andrew W. Howard, Samuel Halverson, Cristobal Petrovich, Isabel Angelo, Guðmundur Stefánsson, Fei Dai, Aaron Householder, Benjamin Fulton, Steven R. Gibson, Arpita Roy, Abby P. Shaum, Howard Isaacson, Max Brodheim, William Deich, Grant M. Hill, Bradford Holden, Daniel Huber, Russ R. Laher, Kyle Lanclos, Joel N. Payne, Erik A. Petigura, Christian Schwab, Josh Walawender, Sharon X. Wang, Lauren M. Weiss, Joshua N. Winn, Jason T. Wright. "Obliquity Constraints for the Extremely Eccentric Sub-Saturn Kepler-1656 b". ApJ, 971, 40 arxiv: 2407.21188.
77Nicholas Saunders, Samuel K. Grunblatt, Ashley Chontos, Fei Dai, Daniel Huber, Jingwen Zhang, Gudmundur Stefansson, Jennifer L. van Saders, Joshua N. Winn, Daniel Hey, Andrew W. Howard, Benjamin Fulton, Howard Isaacson, Corey Beard, Steven Giacalone, Judah van Zandt, Joseph M. Akana Murphey, Malena Rice, Sarah Blunt, Emma Turtelboom, Paul A. Dalba, Jack Lubin, Casey Brinkman, Emma M. Louden, Emma Page, Cristilyn N. Watkins, Karen A. Collins, Chris Stockdale, Thiam-Guan Tan, Richard P. Schwarz, Bob Massey, Steve B. Howell, Andrew Vanderburg, George R. Ricker, Jon M. Jenkins, Sara Seager, Jessie L. Christiansen, Tansu Daylan, Ben Falk, Max Brodheim, Steven R. Gibson, Grant M. Hill, Bradford Holden, Aaron Householder, Stephen Kaye, Russ R. Laher, Kyle Lanclos, Erik A. Petigura, Arpita Roy, Ryan A. Rubenzahl, Christian Schwab, Abby P. Shaum, Martin M. Sirk, Christopher L. Smith, Josh Walawender, Sherry Yeh. "TESS Giants Transiting Giants. VI. Newly Discovered Hot Jupiters Provide Evidence for Efficient Obliquity Damping after the Main Sequence". AJ, 168, 81. arxiv: 2407.21650.
76Steven Giacalone, Fei Dai, J. J. Zanazzi, Andrew W. Howard, Courtney D. Dressing, Joshua N. Winn, Ryan A. Rubenzahl, Theron W. Carmichael, Noah Vowell, Aurora Kesseli, Samuel Halverson, Howard Isaacson, Max Brodheim, William Deich, Benjamin J. Fulton, Steven R. Gibson, Grant M. Hill, Bradford Holden, Aaron Householder, Stephen Kaye, Russ R. Laher, Kyle Lanclos, Joel Payne, Erik A. Petigura, Arpita Roy, Christian Schwab, Abby P. Shaum, Martin M. Sirk, Chris Smith, Guðmundur Stefánsson, Josh Walawender, Sharon X. Wang, Lauren M. Weiss, Sherry Yeh. "The OATMEAL Survey. I. Low Stellar Obliquity in the Transiting Brown Dwarf System GPX-1". Accepted in AJ, arxiv: 2407.21235.
75Marc Hon, Daniel Huber, Yaguang Li, Travis S. Metcalfe, Timothy R. Bedding, Joel Ong, Ashley Chontos, Ryan Rubenzahl, Samuel Halverson, Rafael A. García, Hans Kjeldsen, Dennis Stello, Daniel R. Hey, Tiago Campante, Andrew W. Howard, Steven R. Gibson, Kodi Rider, Arpita Roy, Ashley D. Baker, Jerry Edelstein, Chris Smith, Benjamin J. Fulton, Josh Walawender, Max Brodheim, Matt Brown, Dwight Chan, Fei Dai, William Deich, Colby Gottschalk, Jason Grillo, Dave Hale, Grant M. Hill, Bradford Holden, Aaron Householder, Howard Isaacson, Yuzo Ishikawa, Sharon R. Jelinsky, Marc Kassis, Stephen Kaye, Russ Laher, Kyle Lanclos, Chien-Hsiu Lee, Scott Lilley, Ben McCarney, Timothy N. Miller, Joel Payne, Erik A. Petigura, Claire Poppett, Michael Raffanti, Constance Rockosi, Dale Sanford, Christian Schwab, Abby P. Shaum, Martin M. Sirk, Roger Smith, Jim Thorne, John Valliant, Adam Vandenberg, Shin Ywan Wang, Edward Wishnow, Truman Wold, Sherry Yeh, Ashley Baker, Sarbani Basu, Megan Bedell, Heather M. Cegla, Ian Crossfield, Courtney Dressing, Xavier Dumusque, Heather Knutson, Dimitri Mawet, John O'Meara, Guðmundur Stefánsson, Johanna Teske, Gautam Vasisht, Sharon Xuesong Wang, Lauren M. Weiss, Joshua N. Winn, Jason T. Wright, "Asteroseismology of the Nearby K-Dwarf σ Draconis using the Keck Planet Finder and TESS". Accepted in AJ, arxiv: 2407.21234.
74Ryan A. Rubenzahl, Fei Dai, Samuel Halverson, Andrew W. Howard, Aaron Householder, Benjamin Fulton, Aida Behmard, Steven R. Gibson, Arpita Roy, Abby P. Shaum, Howard Isaacson, Max Brodheim, William Deich, Grant M. Hill, Bradford Holden, Russ R. Laher, Kyle Lanclos, Joel N. Payne, Erik A. Petigura, Christian Schwab, Chris Smith, Guðmundur Stefánsson, Josh Walawender, Sharon X. Wang, Lauren M. Weiss, Joshua N. Winn, Edward Wishnow. "KPF Confirms a Polar Orbit for KELT-18 b". Accepted in AJ, arxiv: 2407.2119.
73Tianjun Gan, Sharon X. Wang, Fei Dai, Joshua N. Winn, Shude Mao, Siyi Xu, Enric Pallé, Jacob L. Bean, Madison Brady, Nina Brown, Cicero Lu, Rafael Luque, Teo Mocnik, Andreas Seifahrt, Guðmundur K. Stefánsson, "The Aligned Orbit of a Hot Jupiter around the M Dwarf TOI-4201". ApJ, 969, 24, arxiv: 2406.12798.
72M. Brady, J. Bean, A. Seifahrt, D. Kasper, R. Luque, G. Stefánsson, J. Stürmer, D. Charbonneau, K. Collins, J. Doty, Z. Essack, A. Fukui, F. Grau Horta, C. Hedges, C. Hellier, J. Jenkins, N. Narita, S. Quinn, A. Shporer, R. Schwarz, S. Seager, K. Stassun, S. Striegel, C. Watkins, J. Winn, R. Zambelli"Early Results from the HUMDRUM Survey: A Small, Earth-mass Planet Orbits TOI-1450A". Accepted in AJ, arxiv: 2405.10400.
71Quang H. Tran, Brendan P. Bowler, William D. Cochran, Samuel Halverson, Suvrath Mahadevan, Joe P. Ninan, Paul Robertson, Guðmundur Stefánsson, Ryan C. Terrien"The Epoch of Giant Planet Migration Planet Search Program. II. A Young Hot Jupiter Candidate around the AB Dor Member HS Psc". AJ, 167, 193, arxiv: 2403.02378.
70M. Cointepas, F. Bouchy, J. M. Almenara, X. Bonfils, N. Astudillo-Defru, H. Knierim, M. Stalport, L. Mignon, N. Grieves, J. Bean, M. Brady, J. Burt, B. L. Canto Martins, K. A. Collins, K. I. Collins, X. Delfosse, J. R. de Medeiros, B.-O. Demory, C. Dorn, T. Forveille, A. Fukui, T. Gan, Y. Gómez Maqueo Chew, S. Halverson, R. Helled, I. Helm, T. Hirano, K. Horne, S. B. Howell, K. Isogai, D. Kasper, K. Kawauchi, J. H. Livingston, B. Massey, R. A. Matson, F. Murgas, N. Narita, E. Palle, H. M. Relles, L. Sabin, N. Schanche, R. P. Schwarz, A. Seifahrt, A. Shporer, G. Stefansson, J. Sturmer, M. Tamura, T.-G. Tan, J. D. Twicken, N. Watanabe, R. D. Wells, F. P. Wilkin, G. R. Ricker, S. Seager, J. N. Winn, J. M. Jenkins, "TOI-663: A newly discovered multi-planet system with three transiting mini-Neptunes orbiting an early M star". A&A, 685, 19.
69S. Dreizler, R. Luque, I. Ribas, V. Koseleva, H. L. Ruh, E. Nagel, F. J. Pozuelos, M. Zechmeister, A. Reiners, J. A. Caballero, P. J. Amado, V. J. S. Béjar, J. L. Bean, M. Brady, C. Cifuentes, M. Gillon, A. P. Hatzes, Th. Henning, D. Kasper, D. Montes, J. C. Morales, C. A. Murray, E. Pallé, A. Quirrenbach, A. Seifahrt, A. Schweitzer, J. Stürmer, G. Stefánsson, J. I. Vico Linares. "Teegarden's Star revisited. A nearby planetary system with at least three planets". A&A, 684, 117, arxiv: 2402.00923.
68A. Bonfanti, M. Brady, T. G. Wilson, J. Venturini, J. A. Egger, A. Brandeker, S. G. Sousa, M. Lendl, A. E. Simon, D. Queloz, G. Olofsson, V. Adibekyan, Y. Alibert, L. Fossati, M. J. Hooton, D. Kubyshkina, R. Luque, F. Murgas, A. J. Mustill, N. C. Santos, V. Van Grootel, R. Alonso, J. Asquier, T. Bandy, T. Bárczy, D. Barrado Navascues, S. C. C. Barros, W. Baumjohann, J. Bean, M. Beck, T. Beck, W. Benz, M. Bergomi, N. Billot, L. Borsato, C. Broeg, A. Collier Cameron, Sz. Csizmadia, P. E. Cubillos, M. B. Davies, M. Deleuil, A. Deline, L. Delrez, O. D. S. Demangeon, B.-O. Demory, D. Ehrenreich, A. Erikson, A. Fortier, M. Fridlund, D. Gandolfi, M. Gillon, M. Güdel, M. N. Günther, A. Heitzmann, Ch. Helling, S. Hoyer, K. G. Isaak, D. Kasper, L. L. Kiss, K. W. F. Lam, J. Laskar, A. Lecavelier des Etangs, D. Magrin, P. F. L. Maxted, C. Mordasini, V. Nascimbeni, R. Ottensamer, I. Pagano, E. Pallé, G. Peter, G. Piotto, D. Pollacco, R. Ragazzoni, N. Rando, H. Rauer, I. Ribas, G. Scandariato, D. Ségransan, A. Seifahrt, A. M. S. Smith, M. Stalport, G. Stefánsson, M. Steinberger, J. Stürmer, Gy. M. Szabó, N. Thomas, S. Udry, E. Villaver, N. A. Walton, K. Westerdorff, T. Zingales."Characterising TOI-732 b and c: New insights into the M-dwarf radius and density valley". A&A, 682, 66, arxiv: 2311.12577.
67Sarah Jiang, Arpita Roy, Samuel Halverson, Chad F. Bender, Carlos Selgas, O. Justin Otor, Suvrath Mahadevan, Guðmundur Stefánsson, Ryan C. Terrien, Christian Schwab."Revisiting ϵ Eridani with NEID: Identifying New Activity-sensitive Lines in a Young K Dwarf Star". AJ, 167, 9, arxiv: 2311.10677.
66Jack Lubin, Xian-Yu Wang, Malena Rice, Jiayin Dong, Songhu Wang, Brandon T. Radzom, Paul Robertson, Gudmundur Stefansson, Jaime A. Alvarado-Montes, Corey Beard, Chad F. Bender, Arvind F. Gupta, Samuel Halverson, Shubham Kanodia, Dan Li, Andrea S.J. Lin, Sarah E. Logsdon, Emily Lubar, Suvrath Mahadevan, Joe P. Ninan, Jayadev Rajagopal, Aripta Roy, Christian Schwab, Jason T. Wright"TOI-1670 c, a 40 day Orbital Period Warm Jupiter in a Compact System, Is Well Aligned". ApJL, 959, 1 arxiv: 2311.16237.
65Abigail Burrows, Samuel Halverson, Jared C. Siegel, Christian Gilbertson, Jacob Luhn, Jennifer Burt, Chad F. Bender, Arpita Roy, Ryan C. Terrien, Selma Vangstein, Suvrath Mahadevan, Jason T. Wright, Paul Robertson, Eric B. Ford, Guðmundur Stefánsson, Joe P. Ninan, Cullen H. Blake, Michael W. McElwain, Christian Schwab, Jinglin Zhao."The death of Vulcan: NEID reveals the planet candidate orbiting HD 26965 is stellar activity". AJ, 167, 5, arxiv: 2404.17494.
64Shubham Kanodia, Caleb I. Cañas, Suvrath Mahadevan, Eric B. Ford, Ravit Helled, Dana E. Anderson, Alan Boss, William D. Cochran, Megan Delamer, Te Han, Jessica E. Libby-Roberts, Andrea S.J. Lin, Simon Müller, Paul Robertson, Guðmundur Stefánsson, Johanna Teske."Searching for Giant Exoplanets around M-dwarf Stars (GEMS) I: Survey Motivation". AJ, 167, 4, arxiv: 2402.04946.
63Megan Delamer, Shubham Kanodia, Caleb I. Cañas, Simon Müller, Ravit Helled, Andrea S.J. Lin, Jessica E. Libby-Roberts, Arvind F. Gupta, Suvrath Mahadevan, Johanna Teske, R. Paul Butler, Samuel W. Yee, Jeffrey D. Crane, Stephen Shectman, David Osip, Yuri Beletsky, Andrew Monson, Jaime A. Alvarado-Montes, Chad F. Bender, Jiayin Dong, Te Han, Joe P. Ninan, Paul Robertson, Arpita Roy, Christian Schwab, Guðmundur Stefánsson, Jason T. Wright. "TOI-4201: An Early M-dwarf Hosting a Massive Transiting Jupiter Stretching Theories of Core-Accretion". ApJL, 962, 22, arxiv: 2307.06880.
62Michael Gully-Santiago, Caroline V. Morley, Jessica Luna, Morgan MacLeod, Antonija Oklopčić, Aishwarya Ganesh, Quang H. Tran, Zhoujian Zhang, Brendan P. Bowler, William D. Cochran, Daniel M. Krolikowski, Suvrath Mahadevan, Joe P. Ninan, Guðmundur Stefánsson, Andrew Vanderburg, Joseph A. Zalesky, Gregory R. Zeimann. "A Large and Variable Leading Tail of Helium in a Hot Saturn Undergoing Runaway Inflation". AJ, 167, 4, arxiv: 2307.08959.
61Juan I. Espinoza-Retamal, Rafael Brahm, Cristobal Petrovich, Andrés Jordán, Guðmundur Stefánsson, Elyar Sedaghati, Melissa J. Hobson, Diego J. Muñoz, Gavin Boyle, Rodrigo Leiva, Vincent Suc. "The Aligned Orbit of the Eccentric Proto Hot Jupiter TOI-3362b". (2023). ApJL, 958, 20, arxiv: 2309.03306.
60Te Han, Paul Robertson, Shubham Kanodia, Caleb Cañas, Andrea S.J. Lin, Guðmundur Stefánsson, Jessica E. Libby-Roberts, Alexander Larsen, Henry A. Kobulnicky, Suvrath Mahadevan, Chad F. Bender, William D. Cochran, Michael Endl, Mark E. Everett, Arvind F. Gupta, Samuel Halverson, Fred Hearty, Andrew Monson, Joe P. Ninan, Arpita Roy, Christian Schwab, Ryan C. Terrien. "TOI-5344 b: A Saturn-like Planet Orbiting a Super-solar Metallicity M0 Dwarf". (2024). AJ, 166, 181, arxiv: 2310.20634.
59Stephanie Yoshida, Shreyas Vissapragada, David W. Latham, Allyson Bieryla, Daniel P. Thorngren, Jason D. Eastman, Mercedes López-Morales, Khalid Barkaoui, Charles Beichmam, Perry Berlind, Lars A. Buchave, Michael L. Calkins, David R. Ciardi, Karen A. Collins, Rosario Cosentino, Ian J.M. Crossfield, Fei Dai, Victoria DiTomasso, Nicholas Dowling, Gilbert A. Esquerdo, Raquel Forés-Toribio, Adriano Ghedina, Maria V. Goliguzova, Eli Golub, Erica J. Gonzales, Ferran Grau Horta, Jesus Higuera, Nora Hoch, Keith Horne, Steve B. Howell, Jon M. Jenkins, Jessica Klusmeyer, Didier Laloum, Jack J. Lissauer, Sarah E. Logsdon, Luca Malavolta, Rachel A. Matson, Elisabeth C. Matthews, Kim K. McLeod, Jennifer V. Medina, Jose A. Muñoz, Hugh P. Osborn, Boris Safonov, Joshua Schlieder, Michael Schmidt, Heidi Schweiker, Sara Seager, Alessandro Sozzetti, Gregor Srdoc, Guđmundur Stefánsson, Ivan A. Strakhov, Stephanie Striegel, Joel Villaseñor, Joshua N. Winn. "TESS Spots a Super-puff: The Remarkably Low Density of TOI-1420b". AJ, 166, 181, arxiv: 2309.09945.
58Rachel Bowens-Rubin, Joseph M. Akana Murphy, Philip M. Hinz, Mary Anne Limbach, Andreas Seifahrt, Rocio Kiman, Maïssa Salama, Sagnick Mukherjee, Madison Brady, Aarynn L. Carter, Rebecca Jensen-Clem, Maaike A.M. van Kooten, Howard Isaacson, Molly Kosiarek, Jacob L. Bean, David Kasper, Rafael Luque, Gudmundur Stefánsson, Julian Stürmer. "A Wolf 359 in Sheep's Clothing: Hunting for Substellar Companions in the Fifth-closest System Using Combined High-contrast Imaging and Radial Velocity Analysis". AJ, 166, 260, arxiv: 2309.03402.
57Lily L. Zhao, Xavier Dumusque, Eric B. Ford, Joe Llama, Annelies Mortier, Megan Bedell, Khaled Al Moulla, Chad F. Bender, Cullen H. Blake, John M. Brewer, Andrew Collier Cameron, Rosario Cosentino, Pedro Figueira, Debra A. Fischer, Adriano Ghedina, Manuel Gonzalez, Samuel Halverson, Shubham Kanodia, David W. Latham, Andrea S.J. Lin, Gaspare Lo Curto, Marcello Lodi, Sarah E. Logsdon, Christophe Lovis, Suvrath Mahadevan, Andrew Monson, Joe P. Ninan, Francesco Pepe, Rachael M. Roettenbacher, Arpita Roy, Nuno C. Santos, Christian Schwab, Guðmundur Stefánsson, Andrew E. Szymkowiak, Ryan C. Terrien, Stephane Udry, Sam A. Weiss, François Wildi, Thibault Wildi, Jason T. Wright. "The Extreme Stellar-signals Project. III. Combining Solar Data from HARPS, HARPS-N, EXPRES, and NEID.". AAS journals (submitted), arxiv: 2309.03762.
56Jiayin Dong, Songhu Wang, Malena Rice, George Zhou, Chelsea X. Huang, Rebekah I. Dawson, Gudmundur K. Stefánsson, Samuel Halverson, Shubham Kanodia, Suvrath Mahadevan, Michael W. McElwain, Jaime A. Alvarado-Montes, Joe P. Ninan, Paul Robertson, Arpita Roy, Christian Schwab, Sarah E. Logsdon, Ryan C. Terrien, Karen A. Collins, Gregor Srdoc, Ramotholo Sefako, Didier Laloum, David W. Latham, Allyson Bieryla, Paul A. Dalba, Diana Dragomir, Steven Villanueva Jr., Steve B. Howell, George R. Ricker, S. Seager, Joshua N. Winn, Jon M. Jenkins, Avi Shporer, David Rapetti. "TOI-1859b: A 64-Day Warm Jupiter on an Eccentric and Misaligned Orbit". ApJL, 951, 29, arxiv: 2305.16495.
55Zhoujian Zhang, Caroline V. Morley, Michael Gully-Santiago, Morgan MacLeod, Antonija Oklopčić, Jessica Luna, Quang H. Tran, Joe P. Ninan, Suvrath Mahadevan, Daniel M. Krolikowski, William D. Cochran, Brendan P. Bowler, Michael Endl, Gudmundur Stefánsson, Benjamin M. Tofflemire, Andrew Vanderburg, Gregory R. Zeimann. "Giant tidal tails of helium escaping the hot Jupiter HAT-P-32 b". Science Advances, arxiv: 2306.0391.
54Maria C. Schutte, Leslie Hebb, John P. Wisniewski, Caleb I. Canas, Jessica E. Libby-Roberts, Andrea S.J. Lin, Paul Robertson, Gudmundur Stefansson. "Measuring the Temperature of Starspots from Multi-Filter Photometry". AJ (accepted), arxiv: 2307.16015.
53Shubham Kanodia, Andrea S. J. Lin, Emily Lubar, Samuel Halverson, Suvrath Mahadevan, Chad F. Bender, Sarah E. Logsdon, Lawrence W. Ramsey, Joe P. Ninan, Gudmundur Stefansson, Andrew Monson, Christian Schwab, Arpita Roy, Leonardo A. Paredes, Eli Golub, Jesus Higuera, Jessica Klusmeyer, William McBride, Cullen Blake, Scott A. Diddams, Fabien Grise, Arvind F. Gupta, Fred Hearty, Michael W. McElwain, Jayadev Rajagopal, Paul Robertson, Ryan Terrien. "Stable fiber-illumination for extremely precise radial velocities with NEID". AJ (accepted), arxiv: 2307.12403.
52Luke C. Powers, Jessica Libby-Roberts, Andrea S.J. Lin, Caleb I. Cañas, Shubham Kanodia, Suvrath Mahadevan, Joe P. Ninan, Guðmundur Stefánsson, Arvind F. Gupta, Sinclaire Jones, Henry A. Kobulnicky, Andrew Monson, Brock A. Parker, Tera N. Swaby, Chad F. Bender, William D. Cochran, Leslie Hebb, Andrew J. Metcalf, Paul Robertson, Christian Schwab, John Wisniewski, Jason T. Wright. "TOI-3785 b: A Low-Density Neptune Orbiting an M2-Dwarf Star". AJ, 166, 44, arxiv: 2304.04730.
51 James Sikora, Jason Rowe, Saugata Barat, Jacob L. Bean, Madison Brady, Jean-Michel Désert, Adina D. Feinstein, Emily A. Gilbert, Gregory Henry, David Kasper, Déreck-Alexandre Lizotte, Michael R. B. Matesic, Vatsal Panwar, Andreas Seifahrt, Hinna Shivkumar, Gudmundur Stefánsson, Julian Stürmer. "Updated Planetary Mass Constraints of the Young V1298 Tau System Using MAROON-X". AJ, 165, 250, arxiv: 2304.00797.
50Mika Lambert, Chad F. Bender, Shubham Kanodia, Caleb I. Cañas, Andrew Monson, Guðmundur Stefánsson, William D. Cochran, Mark E. Everett, Arvind F. Gupta, Fred Hearty, Henry A. Kobulnicky, Jessica E. Libby-Roberts, Andrea S.J. Lin, Suvrath Mahadevan, Joe P. Ninan, Brock A. Parker, Paul Robertson, Christian Schwab, Ryan C. Terrien. "TOI-5375 B: A Very Low Mass Star at the Hydrogen-Burning Limit Orbiting an Early M-type Star". AJ, 165, 218. arxiv: 2303.16193.
49Arvind F. Gupta, Jonathan M. Jackson, Guillaume Hebrard, Andrea S. Lin, Keivan G. Stassun, Jiayin Dong, Steven Villanueva, Diana Dragomir, Suvrath Mahadevan, Jason T. Wright, Jose Manuel Almenara, Cullen H. Blake, Isabelle Boisse, Pia Cortes-Zuleta, Paul A. Dalba, Rodrigo F. Diaz, Eric B. Ford, Thierry Forveille, Robert Gagliano, Samuel P. Halverson, Neda Heidari, Shubham Kanodia, Flavien Kiefer, David W. Latham, Michael W. McElwain, Ismael Mireles, Joshua Pepper, George R. Ricker, Paul Robertson, Arpita Roy, Martin Schlecker, Christian Schwab, Sara Seager, Avi Shporer, Gudmundur Stefansson, Ryan C. Terrien, Eric B. Ting, Joshua N. Winn, Allison Youngblood. "A High-Eccentricity Warm Jupiter Orbiting TOI-4127". AJ, 165, 234. arxiv: 2303.14570.
48Caleb I. Cañas, Chad F. Bender, Suvrath Mahadevan, Dmitry Bizyaev, Nathan De Lee, Scott W. Fleming, Fred Hearty, Steven R. Majewski, Christian Nitschelm, Donald P. Schneider, Javier Serna, Keivan G. Stassun, Guðmundur Stefánsson, Guy S. Stringfellow, John C. Wilson. "Characterization of low-mass companions to Kepler objects of interest observed with APOGEE-N". ApJS, 265, 50. arxiv: 2302.07713.
47Caleb I. Cañas, Shubham Kanodia, Jessica Libby-Roberts, Andrea S.J. Lin, Maria Schutte, Luke Powers, Sinclaire Jones, Andrew Monson, Songhu Wang, Guðmundur Stefánsson, William D. Cochran, Paul Robertson, Suvrath Mahadevan, Adam F. Kowalski, John Wisniewski, Brock A. Parker, Alexander Larsen, Franklin A.L. Chapman, Henry A. Kobulnicky, Arvind F. Gupta, Mark E. Everett, Bryan Edward Penprase, Gregory Zeimann, Corey Beard, Chad F. Bender, Knicole D. Colón, Scott A. Diddams, Connor Fredrick, Samuel Halverson, Joe P. Ninan, Lawrence W. Ramsey, Arpita Roy, Christian Schwab. "TOI-3984 A b and TOI-5293 A b: two temperate gas giants transiting mid-M dwarfs in wide binary systems". AJ (submitted) arxiv: 2302.07714.
46Jessica E. Libby-Roberts, Maria Schutte, Leslie Hebb, Shubham Kanodia, Caleb Canas, Gudmundur Stefansson, Andrea S.J. Lin, Suvrath Mahadevan, Winter Parts (They/Them), Luke Powers, John Wisniewski, Chad F. Bender, William D. Cochran, Scott A. Diddams, Mark E. Everett, Arvind F. Gupta, Samuel Halverson, Henry A. Kobulnicky, Adam F. Kowalski, Alexander Larsen, Andrew Monson, Joe P. Ninan, Brock A. Parker, Lawrence W. Ramsey, Paul Robertson, Christian Schwab, Tera N. Swaby, Ryan C. Terrien. "An In-Depth Look at TOI-3884b: a Super-Neptune Transiting a M4 Dwarf with Persistent Star Spot Crossings". AJ, 165, 249. arxiv: 2302.04757.
45Andrea S.J. Lin, Jessica E. Libby-Roberts, Jaime A. Alvarado-Montes, Caleb I. Cañas, Shubham Kanodia, Leslie Hebb, Eric L. N. Jensen, Suvrath Mahadevan, Luke C. Powers, Tera N. Swaby, John Wisniewski, Corey Beard, Chad F. Bender, Cullen H. Blake, William D. Cochran, Scott A. Diddams, Robert C. Frazier, Connor Fredrick, Michael Gully-Santiago, Samuel Halverson, Sarah E. Logsdon, Michael W. McElwain, Caroline Morley, Joe P. Ninan, Jayadev Rajagopal, Lawrence W. Ramsey, Paul Robertson, Arpita Roy, Christian Schwab, Guðmundur Stefánsson, Daniel J. Stevens, Ryan C. Terrien, Jason T. Wright."The unusual M-dwarf Warm Jupiter TOI-1899~b: Refinement of orbital and planetary parameters". AJ (submitted) arxiv: 2301.10837.
44Madison Brady, Jacob Bean, Andreas Seifahrt, David Kasper, Rafael Luque, Ansgar Reiners, Björn Benneke, Guðmundur Stefánsson, Julian Stürmer. "Measuring the Obliquities of the TRAPPIST-1 Planets with MAROON-X". AJ, 165, 129. arxiv: 2211.11841.
43Casey Brinkman, Lauren M. Weiss, Fei Dai, Daniel Huber, Edwin S. Kite, Diana Valencia, Jacob L. Bean, Corey Beard, Aida Behmard, Sarah Blunt, Madison Brady, Benjamin Fulton, Steven Giacalone, Andrew W. Howard, Howard Isaacson, David Kasper, Jack Lubin, Mason MacDougall, Joseph M. Akana Murphy, Mykhalo Plotnykov, Alex S. Polanski, Malena Rice, Andreas Seifahrt, Gudmundur Stefansson, Julian Sturmer. "TOI-561 b: A Low Density Ultra-Short Period "Rocky" Planet around a Metal-Poor Star". AJ, 165, 88. arxiv: 2210.06665.
42Shubham Kanodia, Suvrath Mahadevan, Jessica Libby-Roberts, Gudmundur Stefansson, Caleb I. Canas, Anjali A. A. Piette, Alan Boss, Johanna Teske, John Chambers, Greg Zeimann, Andrew Monson, Paul Robertson, Joe P. Ninan, Andrea S.J. Lin, Chad F. Bender, William D. Cochran, Scott A. Diddams, Arvind F. Gupta, Samuel Halverson, Suzanne Hawley, Henry A. Kobulnicky, Andrew J. Metcalf, Brock A. Parker, Luke Powers, Lawrence W. Ramsey, Arpita Roy, Christian Schwab, Tera N. Swaby, Ryan C. Terrien, John Wisniewski. "TOI-5205b: A Jupiter transiting an M dwarf near the Convective Boundary". AJ, 165, 120. arxiv: 2209.11160.
41Arvind F. Gupta, Jacob K. Luhn, Jason T. Wright, Suvrath Mahadevan, Eric B. Ford, Gudmundur Stefansson, Chad F. Bender, Cullen H. Blake, Samuel Halverson, Fred R. Hearty, Shubham Kanodia, Sarah E. Logsdon, Michael W. McElwain, Joe P. Ninan, Paul Robertson, Arpita Roy, Christian Schwab, Ryan C. Terrien. "Detection of p-mode Oscillations in HD 35833 with NEID and TESS". AJ, 164, 254. arxiv: 2210.00544.
40P. Chaturvedi, P. Bluhm, E. Nagel, A. P. Hatzes, G. Morello, M. Brady, J. Korth, K. Molaverdikhani, D. Kossakowski, J. A. Caballero, E. W. Guenther, E. Pallé, N. Espinoza, A. Seifahrt, N. Lodieu, C. Cifuentes, E. Furlan, P. J. Amado, T. Barclay, J. Bean, V. J. S. Béjar, G. Bergond, A. W. Boyle, D. Ciardi, K. A. Collins, K. I. Collins, E. Esparza-Borges, A. Fukui, C. L. Gnilka, R. Goeke, P. Guerra, Th. Henning, E. Herrero, S. B. Howell, S. V. Jeffers, J. M. Jenkins, E. L. N. Jensen, D. Kasper, T. Kodama, D. W. Latham, M. J. López-González, R. Luque, D. Montes, J. C. Morales, M. Mori, F. Murgas, N. Narita, G. Nowak, H. Parviainen, V. M. Passegger, A. Quirrenbach, S. Reffert, A. Reiners, I. Ribas, G. R. Ricker, E. Rodríguez, C. Rodríguez-López, M. Schlecker, R. P. Schwarz, A. Schweitzer, S. Seager, G. Stefánsson, C. Stockdale, L. Tal-Or, J. D. Twicken, S. Vanaverbeke, G. Wang, D. Watanabe, J. N. Winn, M. Zechmeister. "TOI-1468: A system of two transiting planets, a super-Earth and a mini-Neptune, on opposite sides of the radius valley". A&A, 666, 155. arxiv: 2208.10351.
39Malena Rice, Songhu Wang, Xian-Yu Wang, Gudmundur Stefansson, Howard Isaacson, Andrew W. Howard, Sarah E. Logsdon, Heidi Schweiker, Fei Dai, Casey Brinkman, Steven Giacalone, Rae Holcomb. "A Tendency Toward Alignment in Single-star Warm-Jupiter Systems". AJ, 164, 104 arxiv: 2207.06511.
38Corey Beard, Paul Robertson, Shubham Kanodia, Jack Lubin, Caleb I. Cañas, Arvind F. Gupta, Rae Holcomb, Sinclaire Jones, Jessica E. Libby-Roberts, Andrea S.J. Lin, Suvrath Mahadevan, Guðmundur Stefánsson, Chad F. Bender, Cullen H. Blake, William D. Cochran, Michael Endl, Mark Everett, Eric B. Ford, Connor Fredrick, Samuel Halverson, Leslie Hebb, Dan Li, Sarah E. Logsdon, Jacob Luhn, Michael W. McElwain, Andrew J. Metcalf, Joe P. Ninan, Jayadev Rajagopal, Arpita Roy, Maria Schutte, Christian Schwab, Ryan C. Terrien, John Wisniewski, Jason T. Wright. "GJ 3929: High-precision Photometric and Doppler Characterization of an Exo-Venus and Its Hot, Mini-Neptune-mass Companion". ApJ, 936, 55 arxiv: 2207.10672.
37 Jiayin Dong, Chelsea X. Huang, George Zhou, Rebekah I. Dawson, Gudmundur K. Stefánsson, Chad F. Bender, Cullen H. Blake, Eric B. Ford, Samuel Halverson, Shubham Kanodia, Suvrath Mahadevan, Michael W. McElwain, Joe P. Ninan, Paul Robertson, Arpita Roy, Christian Schwab, Daniel J. Stevens, Ryan C. Terrien, Andrew Vanderburg, Adam L. Kraus, Stephanie Douglas, Elisabeth Newton, Rayna Rampalli, Daniel M. Krolikowski, Karen A. Collins, Joseph E. Rodriguez, Dax L. Feliz, Gregor Srdoc, Carl Ziegler, Khalid Barkaoui, Francisco J. Pozuelos, Emmanuel Jehin, Michaël Gillon, Zouhair Benkhaldoun, Pablo Lewin, Raquel Forés-Toribio, Jose A. Muñoz, Kim K. McLeod, Fiona Powers Özyurt, Ferran Grau Horta, Felipe Murgas, David W. Latham, Samuel N. Quinn, Allyson Bieryla, Steve B. Howell, Crystal L. Gnilka, David R. Ciardi, Michael B. Lund, Courtney D. Dressing, Steven Giacalone, Arjun B. Savel, Ivan A. Strakhov, Alexander A. Belinski, George R. Ricker, S. Seager, Joshua N. Winn, Jon M. Jenkins, Guillermo Torres, Martin Paegert. "NEID Rossiter-McLaughlin Measurement of TOI-1268b: A Young Warm Saturn Aligned with Its Cool Host Star". ApJ, 926, 7 arxiv: 2201.12836.
36Andreas Seifahrt, Jacob L. Bean, David Kasper, Julian Stürmer, Madison Brady, Robert Liu, Mathias Zechmeister, Gudmundur K. Stefánsson, Ben Montet, John White, Eduardo Tapia, Teo Mocnik, Siyi Xu, Christian Schwab. "MAROON-X: the first two years of EPRVs from Gemini North". SPIE, 12184, 15.
35Arvind F. Gupta, Chad F. Bender, Joe P. Ninan, Sarah E. Logsdon, Shubham Kanodia, Eli Golub, Jesus Higuera, Jessica Klusmeyer, Samuel Halverson, Suvrath Mahadevan, Michael W. McElwain, Christian Schwab, Gudmundur Stefansson, Paul Robertson, Arpita Roy, Ryan C. Terrien, Jason T. Wright"Real-time exposure control and instrument operation with the NEID spectrograph GUI". SPIE, 12189, 20. arxiv: 2210.00550.
34 Arpan Ghosh, Saurabh Sharma, Joe. P. Ninan, Devendra K. Ojha, Bhuwan C. Bhatt, Shubham Kanodia, Suvrath Mahadevan, Gudmundur Stefansson, R. K. Yadav, A. S. Gour, Rakesh Pandey, Tirthendu Sinha, Neelam Panwar, John P. Wisniewski, Caleb I. Canas, Andrea S. J. Lin, Arpita Roy, Fred Hearty, Lawrence Ramsey, Paul Robertson, Christian Schwab. "Gaia 20eae: A Newly Discovered Episodically Accreting Young Star". ApJ, 926, 68. arxiv: 2112.01717.
33 Shubham Kanodia, Jessica Libby-Roberts, Caleb I. Canas, Joe P. Ninan, Suvrath Mahadevan, Gudmundur Stefansson, Andrea S.J. Lin, Sinclaire Jones, Andrew Monson, Brock A. Parker, Henry A. Kobulnicky, Tera N. Swaby, Luke Powers, Corey Beard, Chad F. Bender, Cullen H. Blake, William D. Cochran, Jiayin Dong, Scott A. Diddams, Connor Fredrick, Arvind F. Gupta, Samuel Halverson, Fred Hearty, Sarah E. Logsdon, Andrew J. Metcalf, Michael W. McElwain, Caroline Morley, Jayadev Rajagopal, Lawrence W. Ramsey, Paul Robertson, Arpita Roy, Christian Schwab, Ryan C. Terrien, John Wisniewski, Jason T. Wright. "TOI-3757 b: A low density gas giant orbiting a solar-metallicity M dwarf". AJ, 164, 81. arxiv: 2203.07178.
32 Michael A. Reefe, Rafael Luque, Eric Gaidos, Corey Beard, Peter P. Plavchan, Marion Cointepas, Bryson L. Cale, Enric Palle, Hannu Parviainen, Dax L. Feliz, Jason Eastman, Keivan Stassun, Jonathan Gagné, Jon M. Jenkins, Patricia T. Boyd, Richard C. Kidwell, Scott McDermott, Karen A. Collins, William Fong, Natalia Guerrero, Jose-Manuel Almenara-Villa, Jacob Bean, Charles A. Beichman, John Berberian, Allyson Bieryla, Xavier Bonfils, François Bouchy, Madison Brady, Edward M. Bryant, Luca Cacciapuoti, Caleb I. Cañas, David R. Ciardi, Kevin I. Collins, Ian Crossfield, Courtney D. Dressing, Philipp Eigmueller, Mohammed El Mufti, Emma Esparza-Borges, Akihiko Fukui, Peter Gao, Claire Geneser, Crystal L. Gnilka, Erica Gonzales, Arvind F. Gupta, Sam Halverson, Fred Hearty, Steve B. Howell, Jonathan Irwin, Shubham Kanodia, David Kasper, Takanori Kodama, Veselin Kostov, David W. Latham, Monika Lendl, Andrea Lin, John H. Livingston, Jack Lubin, Suvrath Mahadevan, Rachel Matson, Elisabeth Matthews, Felipe Murgas, Norio Narita, Patrick Newman, Joe Ninan, Ares Osborn, Samuel N. Quinn, Paul Robertson, Arpita Roy, Joshua Schlieder, Christian Schwab, Andreas Seifahrt, Gareth D. Smith, Ahmad Sohani, Guðmundur Stefánsson, Daniel Stevens, Julian Stürmer, Angelle Tanner, Ryan Terrien, Johanna Teske, David Vermilion, Sharon X. Wang, Justin Wittrock, Jason T. Wright, Mathias Zechmeister, Farzaneh Zohrabi. "A close-in puffy Neptune with hidden friends: The enigma of TOI 620". AJ, 163, 269. arxiv: 2204.03108.
31 Corey Beard, Paul Robertson, Shubham Kanodia, Jessica Libby-Roberts, Caleb I. Canas, Arvind F. Gupta, Rae Holcomb, Sinclaire Jones, Henry A. Kobulnicky, Andrea S.J. Lin, Jack Lubin, Marissa Maney, Brock A. Parker, Gudmundur Stefansson, William D. Cochran, Michael Endl, Leslie Hebb, Suvrath Mahadevan, John Wisniewski, Chad F. Bender, Scott A. Diddams, Mark Everett, Connor Fredrick, Samuel Halverson, Fred Hearty, Andrew J. Metcalf, Andrew Monson, Joe P. Ninan, Arpita Roy, Maria Schutte, Christian Schwab, Ryan C Terrien "TOI-1696 and TOI-2136: Constraining the Masses of Two Mini-Neptunes with the Habitable-Zone Planet Finder". AJ, 163, 286. arxiv: 2204.09063.
30 J. A. Caballero, E. Gonzalez-Alvarez, M. Brady, T. Trifonov, T. G. Ellis, C. Dorn, C. Cifuentes, K. Molaverdikhani, J. L. Bean, T. Boyajian, E. Rodriguez, J. Sanz-Forcada, M. R. Zapatero Osorio, C. Abia, P. J. Amado, N. Anugu, V. J. S. Bejar, C. L. Davies, S. Dreizler, F. Dubois, J. Ennis, N. Espinoza, C. D. Farrington, A. Garcia Lopez, T. Gardner, A. P. Hatzes, Th. Henning, E. Herrero, E. Herrero-Cisneros, A. Kaminski, D. Kasper, R. Klement, S. Kraus, A. Labdon, C. Lanthermann, J.-B. Le Bouquin, M. J. Lopez Gonzalez, R. Luque, A. W. Mann, E. Marfil, J. D. Monnier, D. Montes, J. C. Morales, E. Palle, S. Pedraz, A. Quirrenbach, S. Reffert, A. Reiners, I. Ribas, C. Rodriguez-Lopez, G. Schaefer, A. Schweitzer, A. Seifahrt, B. R. Setterholm, Y. Shan, D. Shulyak, E. Solano, K. R. Sreenivas, G. Stefansson, J. Stuermer, H. M. Tabernero, L. Tal-Or, T. ten Brummelaar, S. Vanaverbeke, K. von Braun, A. Youngblood, M. Zechmeister. "A detailed analysis of the Gl 486 planetary system". A&A, 665, 120. arxiv: 2206.09990.
29 Maria C. Schutte, Leslie Hebb, Simon Lowry, John Wisniewski, Suzanne L. Hawley, Suvrath Mahadevan, Brett M. Morris, Paul Robertson, Graeme Rohn, Gudmundur Stefansson. "Modeling Stellar Surface Features on a Subgiant Star with an M-dwarf Companion". AJ, 164, 14. arxiv: 2205.08620.
28 J.G. Winters, R. Cloutier, A.A. Medina, J.M. Irwin, D. Charbonneau, N. Astudillo-Defru, X. Bonfils, A.W. Howard, H. Isaacson, J.L. Bean, A. Seifahrt, J.K. Teske, J.D. Eastman, J.D. Twicken, K.A. Collins, E.L.N. Jensen, S.N. Quinn, M.J. Payne, M.H. Kristiansen, A. Spencer, A. Vanderburg, M. Zechmeister, L.M. Weiss, S.X. Wang, G. Wang, S. Udry, I.A. Terentev, J. Sturmer, G. Stefansson, A. Shporer, S. Shectman, R. Sefako, H.M. Schwengeler, R.P. Schwarz, N. Scarsdale, R.A. Rubenzahl, A. Roy, L.J. Rosenthal, P. Robertson, E.A. Petigura, F. Pepe, M. Omohundro, J.M.A. Murphy, F. Murgas, T. Movcnik, B.T. Montet, R. Mennickent, A.W. Mayo, B. Massey, J. Lubin, C. Lovis, P. Lewin, D. Kasper, S.R. Kane, J.M. Jenkins, D. Huber, K. Horne, M.L. Hill, P. Gorrini, S. Giacalone, B. Fulton, T. Forveille, P. Figueira, T. Fetherolf, C. Dressing, R.F. Diaz, X. Delfosse, P.A. Dalba, F. Dai, C.C. Cortes, I.J.M. Crossfield, J.D. Crane, D.M. Conti, K.I. Collins, A. Chontos, R.P. Butler, P. Brown, M. Brady, A. Behmard C. Beard, N.M. Batalha, J.-M. Almenara. "A Second Planet Transiting LTT 1445A and a Determination of the Masses of Both Worlds". AJ, 163, 168. arxiv: 2107.14737.
27 Caleb I. Cañas, Shubham Kanodia, Chad F. Bender, Suvrath Mahadevan, Guðmundur Stefánsson, William D. Cochran, Andrea S.J. Lin, Hsiang-Chih Hwang, Luke Powers, Andrew Monson, Elizabeth M. Green, Brock A. Parker, Tera N. Swaby, Henry A. Kobulnicky, John Wisniewski, Arvind F. Gupta, Mark E. Everett, Sinclaire Jones, Benjamin Anjakos, Corey Beard, Cullen H. Blake, Scott A. Diddams, Zehao Dong, Connor Fredrick, Elnaz Hakemiamjad, Leslie Hebb, Jessica E. Libby-Roberts, Sarah E. Logsdon, Michael W. McElwain, Andrew J. Metcalf, Joe P. Ninan, Jayadev Rajagopal, Lawrence W. Ramsey, Paul Robertson, Arpita Roy, Jacob Ruhle, Christian Schwab, Ryan C. Terrien, Jason T. Wright "TOI-3714 b and TOI-3629 b: Two gas giants transiting M dwarfs confirmed with HPF and NEID". AJ, 164, 50. arxiv: 2201.09963.
26 Ryan C. Terrien, Allison Keen, Katy Oda, Winter Parts, Guðmundur Stefánsson, Suvrath Mahadevan, Paul Robertson, Joe P. Ninan, Corey Beard, Chad F. Bender, William D. Cochran, Katia Cunha, Scott A. Diddams, Connor Fredrick, Samuel Halverson, Fred Hearty, Adam Ickler, Shubham Kanodia, Jessica E. Libby-Roberts, Jack Lubin, Andrew J. Metcalf, Freja Olsen, Lawrence W. Ramsey, Arpita Roy, Christian Schwab, Verne V. Smith, Ben Turner. "Rotational modulation of spectroscopic Zeeman signatures in low-mass stars". ApJL, 927, 11. arxiv: 2201.11288.
25 L. G. Bouma, J. L. Curtis, K. Masuda, L. A. Hillenbrand, G. Stefansson, H. Isaacson, N. Narita, A. Fukui, M. Ikoma, M. Tamura, A. L. Kraus, E. Furlan, C. L. Gnilka, K. V. Lester, S. B. Howell. "A 38 Million Year Old Neptune-Sized Planet in the Kepler Field". AJ, 163, 121. arxiv: 2112.14776.
24 Andrea S.J. Lin, Andrew Monson, Suvrath Mahadevan, Joe P. Ninan, Samuel Halverson, Colin Nitroy, Chad F. Bender, Sarah E. Logsdon, Shubham Kanodia, Ryan C. Terrien, Arpita Roy, Jacob K. Luhn, Arvind F. Gupta, Eric B. Ford, Fred Hearty, Russ R. Laher, Emily Hunting, William R. McBride, Noah Isaac Salazar Rivera, Jayadev Rajagopal, Marsha J. Wolf, Paul Robertson, Jason T. Wright, Cullen H. Blake, Caleb I. Canas, Emily Lubar, Michael W. McElwain, Lawrence W. Ramsey, Christian Schwab, Gudmundur Stefansson. "Observing the Sun as a star: Design and early results from the NEID solar feed". AJ, 163, 184. arxiv: 2112.05711.
23 Xian-Yu Wang, Malena Rice, Songhu Wang, Bonan Pu, Guðmundur Stefánsson, Suvrath Mahadevan, Steven Giacalone, Zhen-Yu Wu, Thomas M. Esposito, Paul A. Dalba, Arin Avsar, Bradford Holden, Brian Skiff, Tom Polakis, Kevin Voeller, Sarah E. Logsdon, Jessica Klusmeyer, Heidi Schweiker, Dong-Hong Wu, Corey Beard, Fei Dai, Jack Lubin, Lauren M. Weiss, Chad F. Bender, Cullen H. Blake, Courtney D. Dressing, Samuel Halverson, Andrew W. Howard, Daniel Huber, Howard Isaacson, James A. G. Jackman, Joe Llama, Michael W. McElwain, Jayadev Rajagopal, Arpita Roy, Paul Robertson, Christian Schwab, Evgenya L. Shkolnik, Jason Wright, Gregory Laughlin. "SOLES II: The Aligned Orbit of WASP-148b, the Only Known Hot Jupiter with a Nearby Warm Jupiter Companion, from NEID and HIRES". ApJL, 926, 8. arxiv: 2110.08832.
22 Caleb I. Cañas, Suvrath Mahadevan, William D. Cochran, Chad F. Bender, Eric D. Feigelson, C. E. Harman, Ravi Kumar Kopparapu, Gabriel A. Caceres, Scott A. Diddams, Michael Endl, Eric B. Ford, Samuel Halverson, Fred Hearty, Sinclaire Jones, Shubham Kanodia, Andrea S.J. Lin, Andrew J. Metcalf, Andrew Monson, Joe P. Ninan, Lawrence W. Ramsey, Paul Robertson, Arpita Roy, Christian Schwab, Guðmundur Stefánsson. "A hot Mars-sized exoplanet transiting an M dwarf". AJ, 163, 3. arxiv: 2112.03958.
21 Caleb I. Cañas, Suvrath Mahadevan, Chad F. Bender, Noah Isaac Salazar Rivera, Andrew Monson, Corey Beard, Jack Lubin, Paul Robertson, Arvind F. Gupta, William D. Cochran, Connor Fredrick, Fred Hearty, Sinclaire Jones, Shubham Kanodia, Andrea S.J. Lin, Joe P. Ninan, Lawrence W. Ramsey, Christian Schwab, Guðmundur Stefánsson. "An eccentric Brown Dwarf eclipsing an M dwarf". AJ, 163, 89. arxiv: 2112.03959.
20 Shubham Kanodia, Lawrence W. Ramsey, Marissa Maney, Suvrath Mahadevan, Caleb I. Cañas, Joe P. Ninan, Andrew J. Monson, Adam F. Kowalski, Maximos C. Goumas, Gudmundur Stefansson, Chad F. Bender, William D. Cochran, Scott A. Diddams, Connor Fredrick, Samuel P. Halverson, Fred R. Hearty, Steven Janowiecki, Andrew J. Metcalf, Stephen C. Odewahn, Paul Robertson, Arpita Roy, Christian Schwab, Ryan C. Terrien. "High resolution near-infrared spectroscopy of a flare around the ultracool dwarf vB 10". ApJ, 925, 155. arxiv: 2111.14647.
19 R. C Terrien, J. P Ninan, S. A Diddams, S. Mahadevan, S. Halverson, C. Bender, C. Fredrick, F. Hearty, J. Jennings, A. J. Metcalf, A. Monson, A. Roy, C. Schwab, G. Stefansson. "Broadband Stability of the Habitable Zone Planet Finder Fabry-Pérot Etalon Calibration System: Evidence for Chromatic Variation". In: AJ, 161, 252, (June, 2021). arxiv: 2103.08456.
18 A. Seifahrt, J. L. Bean, J. Stürmer, D. Kasper, L. Gers, C. Schwab, M. Zechmeister, G. Stefánsson, B. Montet, L. A. Dos Santos, A. Peck, J. White, E. Tapia. "On-sky commissioning of MAROON-X: A new precision radial velocity spectrograph for Gemini North". In: SPIE, Vol 11447, (June, 2021). arxiv: 2106.02157.
17 S. Kanodia, S. Halverson, J. P. Ninan, S. Mahadevan, G. Stefansson, A. Roy, L. W. Ramsey, C. F. Bender, S. Janowiecki, W. D. Cochran, S. A. Diddams, N. Drory, M. Endl, E. B. Ford, F. Hearty, A. J. Metcalf, A. Monson, P. Robertson, C. Schwab, R. C. Terrien, J. T. Wright. "A Harsh Test of Far-field Scrambling with the Habitable-zone Planet Finder and the Hobby-Eberly Telescope". In: ApJ, 912, 15, (May, 2021). arxiv: 2103.05148.
16 Quang H. Tran, Brendan P. Bowler, William D. Cochran, Michael Endl, Gudmundur Stefansson, Suvrath Mahadevan, Joe P. Ninan, Chad F. Bender, Samuel Halverson, Arpita Roy, Ryan C. Terrien. "The Epoch of Giant Planet Migration Planet Search Program. I. Near-Infrared Radial Velocity Jitter of Young Sun-like Stars". AJ, 161, 173. arxiv: 2101.11005.
15 Arvind F. Gupta, Jason T. Wright, Paul Robertson, Samuel Halverson, Jacob Luhn, Arpita Roy, Suvrath Mahadevan, Eric B . Ford, Chad F. Bender, Cullen H. Blake, Fred Hearty, Shubham Kanodia, Sarah E. Logsdon, Michael W. McElwain, Andrew Monson, Joe P. Ninan, Christian Schwab, Gudmundur Stefansson, Ryan C. Terrien. "Target Prioritization and Observing Strategies for the NEID Earth Twin Survey". AJ, 161, 130. arxiv: 2101.11689.
14 Christian Schwab, Andrew J. Monson, Shubham Kanodia, Emily Lubar, Andrea S. J. Lin, Colin Nitroy, Samuel Halverson, Qian Gong, Ryan C. Terrien, Joe P. Ninan, Chad Bender, Cullen Blake, Frederick R. Hearty, Suvrath Mahadevan, Michael W. McElwain, Paul M. Robertson, Arpita Roy, Gudmundur Stefansson. "The NEID spectrometer: fibre injection system design". In: SPIE, (Dec, 2020).
13 Shubham Kanodia, Joe P. Ninan, Andrew J. Monson, Suvrath Mahadevan, Colin Nitroy, Christian Schwab, Samuel Halverson, Chad F. Bender, Ryan Terrien, Frederick R.Hearty, Emily Lubar, Michael W. McElwain, Lawrence. W. Ramsey, Paul M.Robertson, Arpita Roy, Gudmundur Stefansson, Daniel J. Stevens. "Ghosts of NEID's past". In: SPIE, (Dec, 2020). arxiv: 2012.00182.
12 Keri Hoadley, Christopher Martin, Brian D. Metzger, Mark Seibert, Andrew McWilliam, Ken J. Shen, James D. Neill, Gudmundur Stefansson, Andrew Monson, Bradley E. Schaefer. "A blue ring nebula from a stellar merger several thousand years ago". In: Nature, 587, 387-391 (Nov, 2020). arxiv: 2011.09589.
11 Christian Obermeier, Jana Steuer, Hanna Kellermann, Roberto P. Saglia, Thomas Henning, Arno Riffeser, Ulrich Hopp, Guðmundur Stefansson, Caleb Cañas, Joe P. Ninan, Suvrath Mahadevan, Howard Isaacson, Andrew W. Howard, John H. Livingston, Johannes Koppenhoefer, Ralf Bender. “Following the TraCS of exoplanets with Pan-Planets: Wendelstein-1b and Wendelstein-2". A&A, 639, 130. arXiv: 2005.13560.
10 Arpita Roy, Sam Halverson, Suvrath Mahadevan, Gudmundur Stefansson, Andrew Monson, Sarah E. Logsdon, Chad F. Bender, Cullen H. Blake, Eli Golub, Arvind Gupta, Kurt P. Jaehnig, Shubham Kanodia, Kyle Kaplan, Michael W. McElwain, Joe P. Ninan, Jayadev Rajagopal, Paul Robertson, Christian Schwab, Ryan C. Terrien, Sharon Xuesong Wang, Marsha J. Wolf, and Jason T. Wright. “Solar Contamination in Extreme-precision Radial-velocity Measurements: Deleterious Effects and Prospects for Mitigation”. In: AJ, 159, 161 (April, 2020). arXiv: 2002.09468.
9 Kristine W. F. Lam, Judith Korth, Kento Masuda, Szilárd Csizmadia, Philipp Eigmüller, Gudmundur Stefansson, Michael Endl, Simon Albrecht, Rafael Luque, John H. Livingston, Teruyuki Hirano, Roi Alonso Sobrino, Oscar Barragán, Juan Cabrera, Ilaria Carleo, Alexander Chaushev, William D. Cochran, Fei Dai, Jerome de Leon, Hans J. Deeg, Anders Erikson, Massimiliano Esposito, Malcolm Fridlund, Akihiko Fukui, Davide Gandolfi, Iskra Georgieva, Lucá Gonzalez Cuesta, Sascha Grziwa, Eike W. Guenther, Artie P. Hatzes, Diego Hidalgo, Maria Hjorth, Petr Kabath, Emil Knudstrup, Mikkel N. Lund, Suvrath Mahadevan, Savita Mathur, Pilar Montañes Rodríguez, Felipe Murgas, Norio Narita, David Nespral, Prajwal Niraula, Enric Palle, Martin Pätzold, Carina M. Persson, Jorge Prieto-Arranz, Heike Rauer, Seth Redfield, Ignasi Ribas, Paul Robertson, Marek Skarka, Alexis M. S. Smith, Jan Subjak, Vincent Van Eylen. “It takes two planets in resonance to tango around K2-146”. In: AJ, 159, 120 (March, 2020). arXiv: 1907.11141.
8 Andrew J. Metcalf, Tyler Anderson, Chad F. Bender, Scott Blakeslee, Wesley Brand, David R. Carlson, William D. Cochran, Scott A. Diddams, Michael Endl, Connor Fredrick, Sam Halverson, Dan D. Hickstein, Fred Hearty, Jeff Jennings, Shubham Kanodia, Kyle F. Kaplan, Eric Levi, Emily Lubar, Suvrath Mahadevan, Andrew Monson, Joe P. Ninan, Colin Nitroy, Steve Osterman, Scott B. Papp, Franklyn Quinlan, Larry Ramsey, Paul Robertson, Arpita Roy, Christian Schwab, Steinn Sigurdsson, Kartik Srinivasan, Gudmundur Stefansson, David A. Sterner, Ryan Terrien, Alex Wolszczan, Jason T. Wright, and Gabriel Ycas. “Stellar Spectroscopy in the Near-infrared with a Laser Frequency Comb”. In: Optica, 6, 2 (Feb 2019), p. 233. arXiv: 1902.00500.
7 S. Kanodia, S. Mahadevan, L. W. Ramsey, Stefansson, G. K., A. J. Monson, F. Hearty, S. Blakeslee, E. Lubar, C. F. Bender, J. P. Ninan, D. Sterner, A. Roy, S. P. Halverson, and P. M. Robertson. “Overview of the spectrometer optical fiber feed for the habitable-zone planet finder”. In: SPIE Conference Series. Vol. 10702. SPIE. Aug. 2018, p. 10702. arXiv: 1808.00557.
6 J. P. Ninan, C. F. Bender, S. Mahadevan, E. B. Ford, A. J. Monson, K. F. Kaplan, R. C. Terrien, A. Roy, P. M. Robertson, S. Kanodia, and Stefansson, G. “The Habitable-Zone Planet Finder: improved flux image generation algorithms for H2RG up-the-ramp data”. In: SPIE Conference Series. Vol. 10709. Aug. 2018.
5 S. Halverson, R. Terrien, S. Mahadevan, A. Roy, C. Bender, Stefansson, G. K., A. Monson, E. Levi, F. Hearty, C. Blake, M. McElwain, C. Schwab, L. Ramsey, J. Wright, S. Wang, Q. Gong, and P. Roberson. “A comprehensive radial velocity error budget for next generation Doppler spectrometers”. In: SPIE Conference Series. Vol. 9908. SPIE. Aug. 2016, 99086P. arXiv: 1607.05634 [astro-ph.IM].
4 P. M. Robertson, F. R. Hearty, T. B. Anderson, Stefansson, G. K., E. I. Levi, C. F. Bender, S. Mahadevan, S. P. Halverson, A. J. Monson, L. W. Ramsey, A. Roy, C. Schwab, R. C. Terrien, M. J. Nelson, and B. Blank. “A system to provide sub-milliKelvin temperature control at T 300K for extreme precision optical radial velocimetry”. In: SPIE Conference Series. Vol. 9908. SPIE. Aug. 2016, p. 990862.
3 C. Schwab, N. Jovanovic, T. Feger, M. Bakovic, Y. V. Gurevich, J. Stürmer, R. Apodaca, L. Vanzi, S. Rukdee, J. S. Lawrence, D. W. Coutts, N. Cvetojevic, S. Mahadevan, Stefansson, G. K., S. P. Halverson, and O. Guyon. “Adaptive optics fed single-mode spectrograph for high-precision Doppler measurements in the near-infrared”. In: SPIE Conference Series. Vol. 9912. SPIE. July 2016, p. 991274.
2 F. Hearty, E. Levi, M. Nelson, S. Mahadevan, A. Burton, L. Ramsey, C. Bender, R. Terrien, S. Halverson, P. Robertson, A. Roy, B. Blank, K. Blanchard, and Stefansson, G. “Environmental control system for Habitable-zone Planet Finder (HPF)”. In: vol. 9147. SPIE. 2014,
1 S. Mahadevan, L. W. Ramsey, R. Terrien, S. Halverson, A. Roy, F. Hearty, E. Levi, Stefansson, G. K., P. Robertson, C. Bender, C. Schwab, and M. Nelson. “The Habitable-zone Planet Finder: A status update on the development of a stabilized fiber-fed near-infrared spectrograph for the for the Hobby-Eberly telescope”. In: Ground-based and Airborne Instrumentation for Astronomy V. Vol. 9147. SPIE. July 2014, 91471G.
Teaching and Mentoring
Mentoring (current)
- Elise Koo, PhD student at University of Amsterdam
- Juan Ignacio Espinoza Retamal, visiting PhD student at University of Amsterdam
- Rowen Glusman, Masters student at University of Amsterdam
- David Bruijne, Masters student at University of Amsterdam
- Hugo Veldhuis, Masters student at University of Amsterdam
- Kaya Han Taş, Masters student at University of Amsterdam
- Onė Mikulskytė, Masters student at University of Amsterdam
- Evan Fitzmaurice, PhD student at Penn State
- Megan Delamer, PhD student at Penn State
Mentoring (previous)
- Yiri Zwart, Bachelor Student at University of Amsterdam
- Robert Frazier (undergraduate at Penn State, incoming graduate student at University of Michigan)
- Sinclaire Jones (undergraduate at Princeton, now graduate student at Ohio State University)
- Marissa Maney (undergraduate at Penn State, now graduate student at Harvard)
- Yiting Li (undergraduate at Penn State, graduate student at UCSB)
Teaching
Spring 2014
- Astro 11 (008) Elementary Astronomy Laboratory, Instructor of Record.
- Rooftop and Planetarium TA
Fall 2013
- Astro 11 (004) Elementary Astronomy Laboratory, Instructor of Record.
- Astro 1 (001) Astronomical Universe, taught by Prof Ravi Kopparapu.
- Astro 1 (004) Astronomical Universe, taught by Prof Eric Feigelson.
- Astro 10 (001) Elementary Astronomy, taught by Prof Alex Wolszczan.
Spring 2013
Physics 2V Experimental Labs in Physics 2V. Supervisors: Prof S. Þ. Ingvarsson and A. Ólalfsson
Fall 2012
Physics 305G Classical Mechanics, taught by Prof P. Jakobsson.
About Me
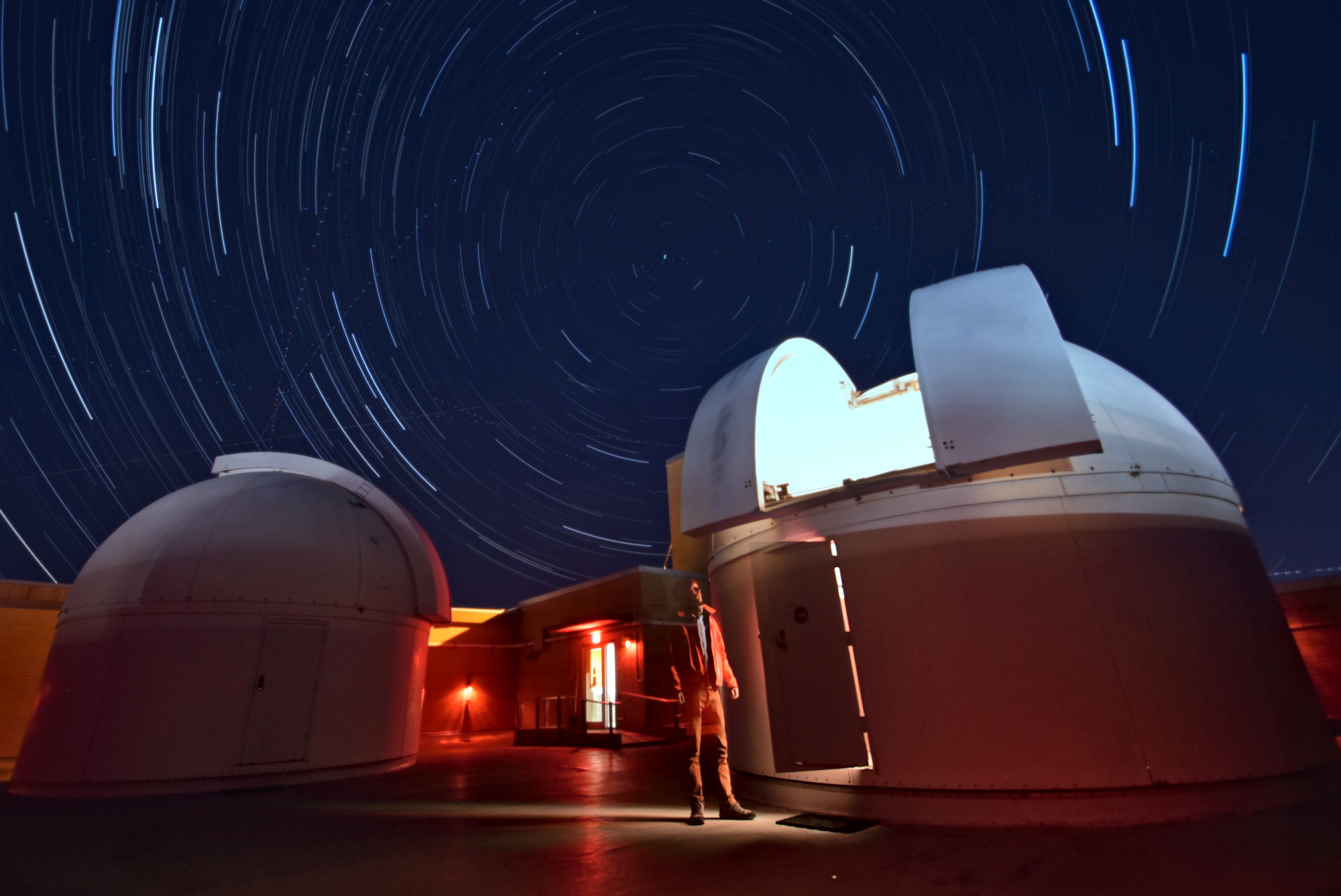
I am an astrophysicist who develops and uses next-generation instruments to better detect and characterize planets orbiting nearby stars, with a particular focus on planets orbiting low-mass stars. To study these worlds, I use two precision radial velocity spectrographs I helped design and deploy—the near-infrared Habitable-zone Planet Finder (HPF) on the 10m Hobby-Eberly Telescope, and the optical NEID spectrograph on the 3.5m WIYN Telescope—along with the diffuser-assisted photometry technique, a low-cost method I have shown is capable of approaching space-quality photometry from the ground.
I am currently a faculty member at the Anton Pannekoek Institute for Astronomy at the University of Amsterdam. Before that, I was a NASA Sagan Fellow (2022-2023) and a Henry Norris Russell Fellow (2019-2022) at the Department of Astrophysical Sciences at Princeton University. I obtained my PhD in Astronomy and Astrophysics at Penn State University in September 2019, where I completed my thesis "Extreme Precision Photometry and Radial Velocimetry from the Ground" supervised by Professor Suvrath Mahadevan as a NASA Earth and Space Science Fellow (2016-2019). My thesis was recognized by the 2020 Robert J Trumpler Award for a PhD thesis deemed unusually important to astronomy. I completed my Bachelor's degree in Physics at the University of Iceland in 2013 where I worked in the Leosson lab in experimental nanophotonics with applications in biosensing, and spent a summer at Stanford University as part of the Summer International Honors Program.
If you have any questions, please don't hesitate to email me at g.k.stefansson - at - uva.nl